徐春玲 張 惠 魯繼利 朱 建
(山東鋼鐵股份有限公司萊蕪分公司煉鐵廠)
摘 要 本文主要介紹了萊蕪分公司煉鐵廠265m2燒結(jié)系統(tǒng)為提高燒結(jié)礦FeO穩(wěn)定性,分析流程可控因子,對(duì)燃料水分、燃料粒度、混勻料水分、四輥破碎質(zhì)量、下料波動(dòng)等進(jìn)行了系列改善,試驗(yàn)分析、探測(cè)關(guān)鍵因子最佳控制水平,優(yōu)化控制區(qū)間,使燒結(jié)礦FeO西格瑪水平達(dá)到3.37,綜合合格率98%以上。
關(guān)鍵詞 燒結(jié)礦 焦粉 噪音因子 固定碳
1 前言
燒結(jié)礦的質(zhì)量指標(biāo)中,F(xiàn)eO含量是影響高爐爐況順行的一個(gè)非常重要的參數(shù),燒結(jié)礦FeO含量的波動(dòng)區(qū)間越窄,燒結(jié)過程越穩(wěn)定。在生產(chǎn)中適當(dāng)降低燒結(jié)礦中的FeO含量,并提高其穩(wěn)定性,既可以保證燒結(jié)礦的冷強(qiáng)度和低溫還原粉化性能,又改善了燒結(jié)礦的還原性,使燒結(jié)礦的冶金性能得到改善,也有利于降低燒結(jié)固體燃耗、高爐焦比。萊蕪分公司煉鐵廠265m2燒結(jié)機(jī),2018年燒結(jié)礦FeO為2.07西格瑪水平且均值高達(dá)8.9%。為提高燒結(jié)礦穩(wěn)定性,進(jìn)而優(yōu)化高爐爐料結(jié)構(gòu),提高高爐爐況穩(wěn)定性,降低高爐煉鐵燃料比和噸鐵成本, 2019年立項(xiàng)攻關(guān)改進(jìn),改善后提升至3.37西格瑪水平且均值降低0.46%。
2 關(guān)鍵影響因素分析
2.1 工藝流程分析
分析燒結(jié)工藝流程(見圖1),流程不可控部分主要在于原鐵礦粉、部分熔劑等原料的源頭采購(gòu),經(jīng)團(tuán)隊(duì)分析對(duì)流程影響程度后,流程可控度大于80%。
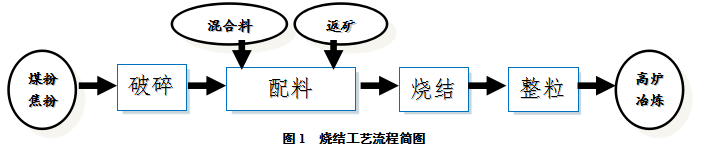
通過流程圖分析得出可控因子9個(gè):燃料水分波動(dòng)、燃料大粒度多、燃料來料質(zhì)量差、混勻料水分波動(dòng)、燒結(jié)料面不平整、四輥破碎質(zhì)量差、燃料配加人為判斷不準(zhǔn)、配料電子稱誤差反饋偏差、燒結(jié)終點(diǎn)溫度控制不當(dāng)。
2.2 部分因子快速改善
2.2.1 燃料水分波動(dòng)
焦粉受料口無噴淋降塵設(shè)備,小焦篩區(qū)域除塵能力有限,上料容易造成揚(yáng)塵。為降低焦粉揚(yáng)塵,常采用水管直接噴灑焦粉方式。水管直接噴淋不均勻,用水量大,容易造成局部焦粉占水過濕。為此,增加霧化噴淋,卸焦粉時(shí)利用霧化噴淋降塵,避免焦粉揚(yáng)塵,焦粉無明顯潤(rùn)濕情況。(改善效果見圖2)
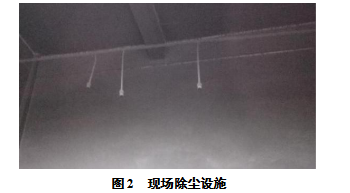
2.2.2 燃料大粒度多
燒結(jié)用焦粉來自焦化篩下焦粉、5、6號(hào)高爐槽下焦粉,燃料來源點(diǎn)多,焦粉經(jīng)?;烊氪罅6冉箟K,增加燒結(jié)燃料破碎難度。造成原因有:高爐、焦化對(duì)焦粉篩維護(hù)不足,造成焦塊混入;崗位人員清掃衛(wèi)生、清除現(xiàn)場(chǎng)落料不規(guī)范,焦塊混入焦粉;燒結(jié)區(qū)小焦篩磨損,造成大粒度焦塊進(jìn)入破碎工序。為此,年修期間對(duì)槽下小焦篩更換篩板,提高大塊焦粉篩出率,避免大塊焦粒進(jìn)入四輥破碎。改進(jìn)后燃料粒度趨于穩(wěn)定,大粒度焦塊明顯減少(改進(jìn)效果見圖3)。
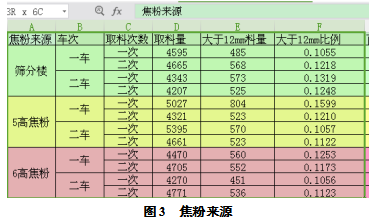
2.2.3 混勻料水分波動(dòng)
混勻料水分受加水水壓、返礦料溫、白灰等因素影響,控制不穩(wěn)定,造成燒結(jié)過程波動(dòng),影響燒結(jié)礦FeO穩(wěn)定,且監(jiān)督控制點(diǎn)全在一混,控制能力較低。在看火崗位增加水分自動(dòng)控制監(jiān)測(cè)裝置,對(duì)水壓、加水量、水分直接監(jiān)測(cè);制定可靠的水分控制標(biāo)準(zhǔn),實(shí)現(xiàn)看火對(duì)水分的小范圍直接控制調(diào)整,提高控制穩(wěn)定性。
2.2.4 燒結(jié)料面不平整
燒結(jié)機(jī)泥輥下料口擋板磨損嚴(yán)重,造成料面布料不平整。利用檢修期更換泥輥下料口擋板。燒結(jié)機(jī)六輥一根棍子損壞,減速箱內(nèi)部齒輪有損壞,造成燒結(jié)料面布料呈波浪狀,布料不平整。檢修更換六輥設(shè)備(改善前后對(duì)比見圖4)。
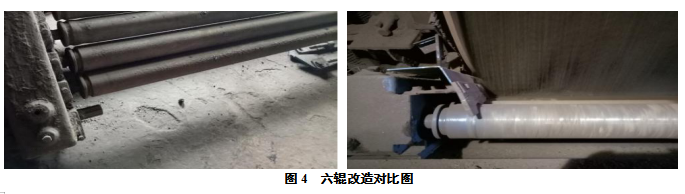
2.2.5 四輥破碎質(zhì)量差
四輥維護(hù)不及時(shí),維護(hù)人員中途更換,對(duì)車削質(zhì)量把關(guān)不嚴(yán)。車削周期不固定、磨損量車削量標(biāo)準(zhǔn)不固定。為此,規(guī)范三臺(tái)四輥破碎機(jī)循環(huán)使用,每周做一次定尺車削。規(guī)范四輥維護(hù)后,燃料破碎良好,燃料粒度3mm粒級(jí)保持80%以上。
2.3 其他因子實(shí)驗(yàn)分析
2.3.1 噪聲因子
噪聲因子來自四輥破碎燃料破碎質(zhì)量、配料室、看火崗位操作人員水平差異,對(duì)燒結(jié)礦FeO的預(yù)知預(yù)控條件上不可改變,部分受控。經(jīng)過方差分析,四個(gè)班組間操作無明顯差異,F(xiàn)eO均值在8.32-8.55之間;但每班之間仍有輕微差異(見圖5),丁班均值較低但標(biāo)準(zhǔn)差略高于其他班組,且四班內(nèi)FeO波動(dòng)仍很明顯。因此,為進(jìn)一步減少班組之間操作上的差異,除加強(qiáng)班組學(xué)習(xí)培訓(xùn)之外,借鑒防錯(cuò)法思想,制定統(tǒng)一操作標(biāo)準(zhǔn),對(duì)影響操作的關(guān)鍵參數(shù)料批數(shù)通過控制圖進(jìn)行監(jiān)控,并進(jìn)行量化操作。
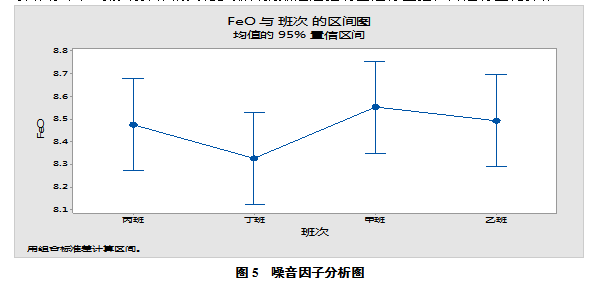
2.3.2 試驗(yàn)因子
配料下料誤差與人為判斷燃料配加量存在部分交互作用,需進(jìn)行組合的檢驗(yàn);燃料質(zhì)量細(xì)分為燃料粒度和固定碳。試驗(yàn)因子統(tǒng)計(jì)見表1。

建立回歸方程,模型回歸P值=0小于0.05(見圖6),回歸模型顯著。其中:燃料粒度P0.869和終點(diǎn)溫度P0.680均大于0.05,效果不顯著,需逐步去除燃料粒度和終點(diǎn)溫度后再做回歸分析。去除燃料粒度建立回歸方程模型回歸P值=0小于0.05,回歸模型顯著,但其中終點(diǎn)溫度P0.677均大于0.05,效果仍不顯著(見圖7);去除燒結(jié)終點(diǎn)溫度建立回歸方程,模型回歸P值=0小于0.05,回歸模型顯著,但終點(diǎn)溫度P0.877均大于0.05,效果仍不顯著(見圖8)。

同時(shí)去除燃料粒度、燒結(jié)終點(diǎn)溫度,第四次建立回歸方程為:燒結(jié)礦FeO% = -6.48 + 2.291 燃料配加量+ 0.0934 燃料固定碳含量%。模型回歸P值=0小于0.05,各項(xiàng)P值也均小于0.05,回歸模型顯著(見圖9);但R-sq71.33%、R-sq(調(diào)整)68.02% 水平仍較低?;貧w方程存在誤差??紤]實(shí)際生產(chǎn)中,燃料粒度對(duì)燒結(jié)礦亞鐵有較明顯影響,仍考慮作為重要因子做進(jìn)一步分析。燒結(jié)終點(diǎn)溫度控制,技術(shù)要求較嚴(yán)格,生產(chǎn)中可通過減機(jī)速,降低布料等措施預(yù)防。可控性較高。
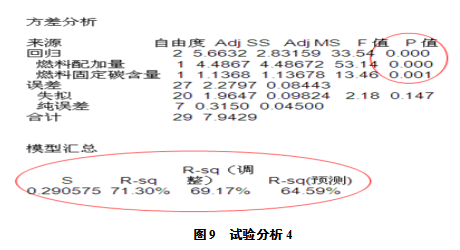
3 關(guān)鍵因子控制
3.1 最佳水平探測(cè)
選取1709批號(hào)料堆做最佳水平探測(cè)試驗(yàn),燃料指標(biāo)分析(燃料配加量2.8-3.3、燃料固定碳80-85%、燃料粒度74-82%),確認(rèn)一元回歸模型預(yù)測(cè)數(shù)據(jù)可靠,通過分析燃料配加量、燃料固定碳、燃料粒度參數(shù),找出與燒結(jié)礦氧化亞鐵對(duì)應(yīng)關(guān)系。試驗(yàn)水平設(shè)定方案見表2。
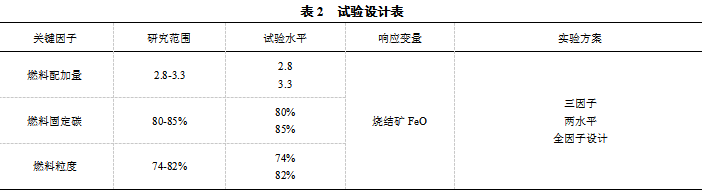
全因子分析結(jié)果:主效應(yīng)P=0.000<0.05,說明模型總體有效;2.S=0.089,R-Sq=98.52%,R-Sq(調(diào)整)=96.75%,模型有效;燃料固定碳與燃料粒度二階交作用顯著,盡管燃料粒度主效應(yīng)不顯著,但仍須保留(見圖10)。

通過曲面圖和等值線分析得出:系統(tǒng)改進(jìn)后,在滿足燒結(jié)礦氧化亞鐵8.0-8.6區(qū)間時(shí),燃料量取值2.9-3.3、固定碳取值80.5-85%、燃料粒度74%-82%,滿足可控制要求。
3.2 燃料下料量波動(dòng)改善
燃破圓盤給料出料口盤面上積料、帶料,嚴(yán)重時(shí)(大料流、物料粘濕或粒度細(xì)小等)盤面周邊頻繁撒料;且圓盤最大出料能力50%達(dá)不到25t/h,達(dá)不到工藝標(biāo)準(zhǔn)要求值。為此,借鑒同行業(yè)經(jīng)驗(yàn),在盤面焊接0.5m鋼筋;出料口長(zhǎng)寬擴(kuò)大,上邊角弧度光滑。改進(jìn)后圓盤最大出料能力100%達(dá)到35t/h,且出料口盤面上出料順暢,無積料、帶料,盤面周邊無撒料現(xiàn)象。原配料7#、8#使用時(shí)間較長(zhǎng),維護(hù)調(diào)整不及時(shí),設(shè)定電子稱量程1.5-5.0,下料量波動(dòng)幅度大,實(shí)際下料誤差在10%以上,遠(yuǎn)遠(yuǎn)超出工藝要求4%。對(duì)配料7#、8#倉(cāng)電子稱更換,更換原頻率調(diào)整燃料下料量方式,采取重量設(shè)定方式,下料準(zhǔn)確,平均誤差控制在3%以內(nèi)。
4 改進(jìn)效果
4.1 燒結(jié)礦FeO
最佳效果顯著性驗(yàn)證:取改善前(5月)和改善后(10月)的數(shù)據(jù),進(jìn)行雙樣本T檢驗(yàn)(樣本量85)。統(tǒng)計(jì)結(jié)論:燒結(jié)礦FeO均值降低0.46 (見圖12),質(zhì)量波動(dòng)明顯降低。
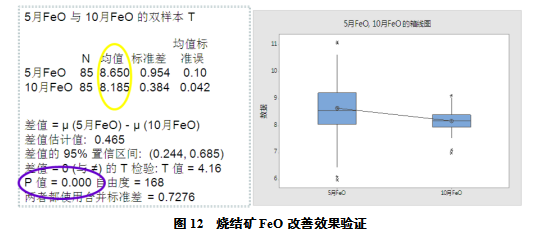
4.2 燒結(jié)礦低溫還原粉化率
取改善前(5月)和改善后(10月)燒結(jié)礦低溫還原粉化率數(shù)據(jù),進(jìn)行雙樣本T檢驗(yàn)(樣本量31)。統(tǒng)計(jì)結(jié)論:改善前后對(duì)比燒結(jié)礦低溫還原粉化率差異不大,燒結(jié)礦FeO適當(dāng)降低,未對(duì)低溫還原粉化率造成影響(見圖13)。
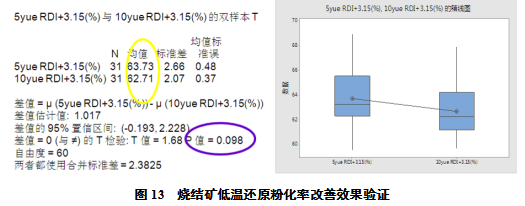
5 結(jié)論
燒結(jié)礦FeO質(zhì)量穩(wěn)定,可有效減少高爐爐況波動(dòng),保證高爐生產(chǎn)穩(wěn)定。原生產(chǎn)操作僅追求燒結(jié)礦FeO合格率,未對(duì)燒結(jié)礦質(zhì)量穩(wěn)定做有效控制,造成燒結(jié)礦FeO存在較大波動(dòng)。經(jīng)過項(xiàng)目團(tuán)隊(duì)系列改進(jìn)實(shí)施,主要通過對(duì)燒結(jié)燃料粒度有效控制、固化燃料調(diào)整等措施,加強(qiáng)燒結(jié)過程控制,提高燒結(jié)礦成分穩(wěn)定性。燒結(jié)礦FeO西格瑪水平達(dá)到3.37,綜合合格率98%以上,超額完成預(yù)期目標(biāo),對(duì)同行業(yè)具有加大的推廣價(jià)值。