左海濱,張建良,王筱留
(北京科技大學冶金與生態(tài)工程學院)
摘 要:從分析目前高爐煉鐵碳消耗的本質出發(fā),針對給定的原燃料條件,利用模型計算分析了當前主要低碳煉鐵途徑的節(jié)碳潛力。結果表明:對于普通高爐而言,間接還原達到平衡時的煤氣利用率為56.99%,降低燃料比28.37kg/t。氧氣高爐爐頂煤氣完全循環(huán)利用條件下,最低燃料比為385.6kg/t。噴吹焦爐煤氣可以降低燃料比,每增加10m3噴吹量,可降低焦比5.0kg/t左右;此外噴吹量存在極值,隨著富氧率提高,獲得最低燃料比的噴吹量增大,且最低燃料比降低。最佳噴吹條件為富氧率6%~8%,噴吹量160~180m3/t,可節(jié)約焦比53~54kg/t。使用高反應性焦炭可以降低熱儲備區(qū)溫度,使間接還原平衡時CO濃度降低,平衡CO濃度從70%~60%,每降低2.5%,理論上可降低燃料消耗10.3~12.2kg/t,且降低幅度逐漸減小。
關鍵詞:低碳煉鐵;氧氣高爐;煤氣循環(huán);高反應性焦炭
據(jù)統(tǒng)計,近幾年內每年中國工業(yè)能源消耗總量約為20億t標準煤,其中鋼鐵工業(yè)消耗高于3億標準煤(含礦山、鐵合金、焦化、耐材等),占中國工業(yè)能源總消耗量的15%以上,是能耗最高的行業(yè)。此外,鋼鐵冶金是基于碳的高溫冶金過程,因此,鋼鐵工業(yè)每年產生大量的溫室氣體CO2以及多種大氣污染物,如硫氧化物、氨氧化物、各種煙塵和粉塵等,溫室氣體排放占全國工業(yè)總排放量的10.5%,因此鋼鐵工業(yè)的節(jié)能減排意義重大。降低煉鐵過程碳素消耗是實現(xiàn)鋼鐵工業(yè)節(jié)能減排的主要途徑。中國鋼鐵生產的能源結構中煤炭占到70%,它在高爐煉鐵方面就是燃料消耗。而降低煤炭消耗量的途徑一是尋求替代品,二是提高煤炭在冶煉過程中的利用率[1-3]有鑒于此,近年來國內外眾多冶金學者熱衷于全氧高爐[4-5]、焦爐煤氣噴吹[6-8]以及高反應性焦炭應用[9-10]利用一個具體實例分析不同工藝條件下節(jié)能的潛力,并對各工藝的關鍵限制性環(huán)節(jié)進行探討。
1. 高爐能量消耗分析及模型計算條件
高爐煉鐵是以焦炭為主要燃料的高溫火法冶煉,屬碳冶金學,即以碳作為冶煉過程的還原劑和熱源,冶煉的產品是Fe-C合金——生鐵。同時又以焦煤、肥煤、氣煤及其它煤配合成混合煤煉制的焦炭作為高爐料柱骨架,保證高爐冶煉順利進行,其用量決定著高爐煉鐵的經濟性。這樣高爐冶煉過程消耗一定量的碳,而生產結果除生鐵和爐渣外,還產生CO和CO2。其中CO又在熱風爐、加熱爐、鍋爐燃燒過后成為CO2:溶解在鐵水中的C在煉鋼過程中又氧化成CO成為轉爐煤氣,轉爐煤氣作為氣體燃料在用戶處再氧化成CO2。從一次能耗來說,高爐冶煉的焦比、燃料比決定了碳的消耗和排放的CO2量。盡管根據(jù)能量守恒原理,所有高爐消耗的燃料除滿足最低的高爐能量需求外,都將轉化成為其他不同形式的能量,但由于有些轉化后的能量品質下降,不能被充分利用或者在利用形式上導致能源效率降低,進而造成能量的浪費。因此降低燃料比仍是高爐工作者的不斷追求。
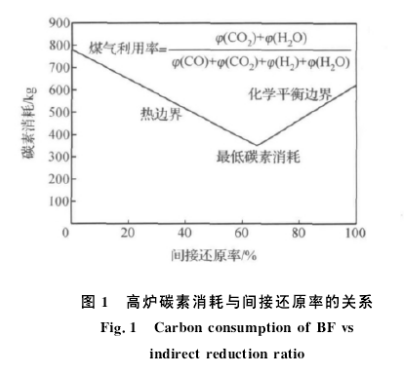
目前國內外煉鐵界判斷碳消耗的高低是使用C-rd或C-ri圖,德國蒂森公司使用的C-ri圖如圖1所示。高爐理論最低碳消耗的條件為直接還原生成的CO和為維持高爐煉鐵順利進行所需碳素燃燒提供熱量產生的CO之和剛好滿足間接還原所需CO量。而實際生產中,往往由于礦石還原性差或氣流分布問題造成間接還原不足,直接還原度升高,高爐上的直接表現(xiàn)為煤氣利用率低。此外爐渣熱熔偏大建立高爐能量利用分析模型,該模型可以針對全氧鼓風——爐頂煤氣循環(huán)、焦爐煤氣噴吹以及高反應性焦炭應用等各種工藝條件進行計算。本文以國內某高爐原燃料條件為例進行計算,分析比較不同工藝的能量利用狀況。高爐原、燃料條件見表1和表2。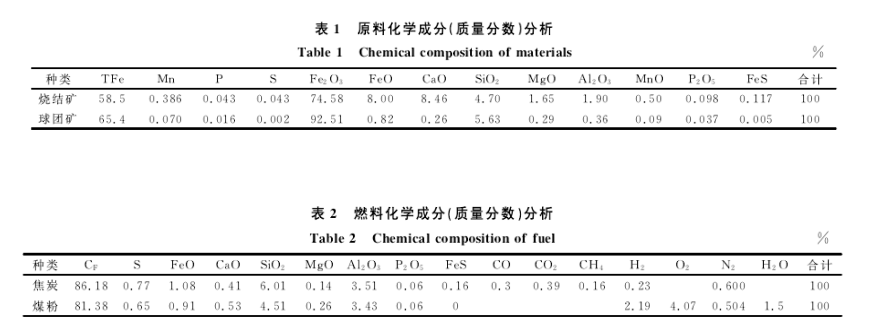
2. 不同工藝條件計算結果分析
2.1普通高爐
對如表3所示普通高爐生產條件下的物料消耗和能量利用進行計算分析,為便于比較,爐體散熱損失統(tǒng)一按照熱收入的5%考慮。計算燃料比時,固定焦比320kg/t,根據(jù)熱量平衡計算煤比,進而得到燃料比。礦石消耗量根據(jù)鐵平衡和堿度平衡方程聯(lián)立求解。計算結果如表4和表5所示。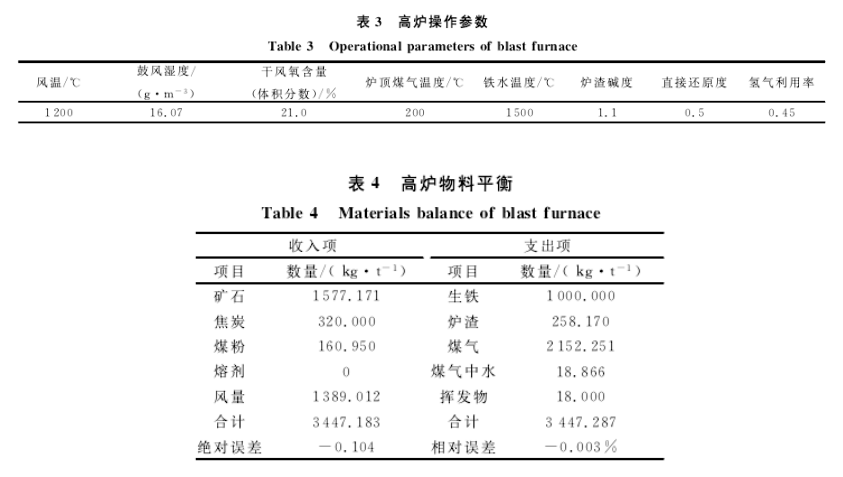
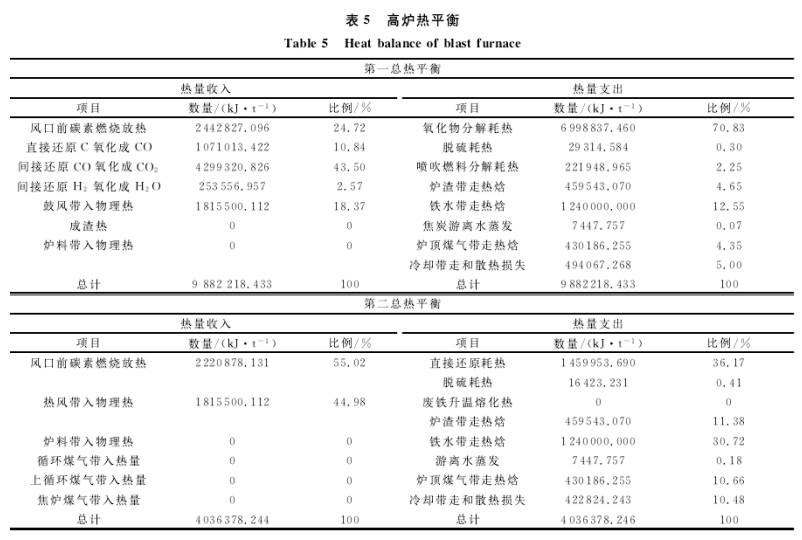
計算得到燃料比為480.95kg/t,根據(jù)爐頂煤氣成分計算煤氣利用率為50.35%,輸出煤氣量為1553.87m3,煤氣熱值為2880.5kJ/m3。計算進一步降低燃料比的潛力,即達到上述理論最低碳素消耗的情況,得到直接還原度為0.4503,燃料比為452.58kg/t,煤氣利用率為56.99%,可節(jié)約燃耗2837kg,折合碳耗23.09kg。間接還原反應是否能接近平衡取決于原料條件和操作水平。不同煤氣利用率條件下碳素消耗和直接還原度的關系如圖2所示。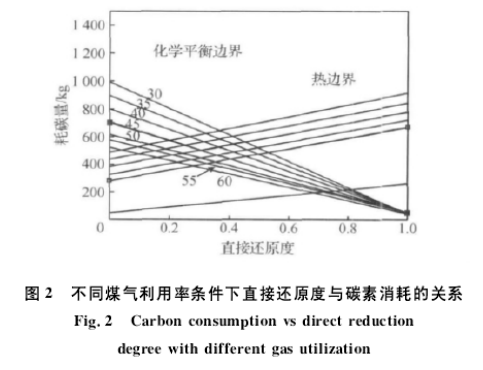
從圖2中看出,隨著煤氣利用率提高,間接還原反應接近平衡,高爐燃料比降低,最低碳消耗隨著噸鐵熱量需求的降低而降低。此外值得注意的是,在相同煤氣利用率條件下,高爐最低碳消耗對應的直接還原度是隨著噸鐵熱量需求的降低而有所增加。這是因為隨著噸鐵熱量需求的降低,為提供熱量燃燒的碳量減少,為滿足間接還原所需CO量,需要增加直接還原度來提供所需的CO,同時直接還原消耗的熱量仍要由碳的燃燒提供,但此時作為還原劑和提供熱量消耗的碳量之和要小于噸鐵總熱量需求減少引起的碳消耗減少量,因此直接還原度略有增加。
2.2全氧高爐
氧氣高爐工藝是利用常溫的純氧代替熱風鼓風。從表5高爐的熱平衡可以看出,鼓風帶入的顯熱為1.8155GJ,而采用常溫純氧代替熱風時,這部分熱量就需要由碳在高爐內的燃燒提供,這勢必造成燃料比的升高。因此全氧鼓風必須和爐頂煤氣循環(huán)結合。從本質上講,氧氣高爐實際上是利用脫除CO2的循環(huán)煤氣代替常規(guī)高爐鼓風中的N,提高煤氣還原勢,進而提高間接還原度,降低直接還原耗碳和熱量消耗,從而彌補缺少的熱風顯熱。按照鐵水中鐵的質量分數(shù)為94.5%計算,直接還原度降低Q1,還原節(jié)約的碳量為20.25kg,減少直接還原耗熱折合碳量為26.15kg,總計46.40kg。假設直接還原度由0.5降低到0.2,則節(jié)約碳量折合熱量為1.36GJ,與鼓風顯熱相比,仍有0.45GJ的差距,這就需要其他的能量來源。當然由于采用全氧鼓風,噸鐵煤氣量將有所減小,煤氣帶走的顯熱減少。因此,從高爐噸鐵熱量需求上考慮,氧氣高爐降低燃料比的途徑一是降低噸鐵熱消耗,主要通過降低直接還原度、減少噸鐵煤氣量實現(xiàn);二是通過加熱循環(huán)煤氣補充熱量。為便于比較,計算過程中固定熱損失為熱收入的5%,選代過程中要滿足爐頂煤氣和循環(huán)煤氣中CO、H2以及N2。的相對比例保持不變。為保證焦炭的骨架作用,焦比下限定為250kg/t。同時控制理論燃燒溫度在2000~2300℃之間。采用單排風口工藝時的計算結果如表6所示。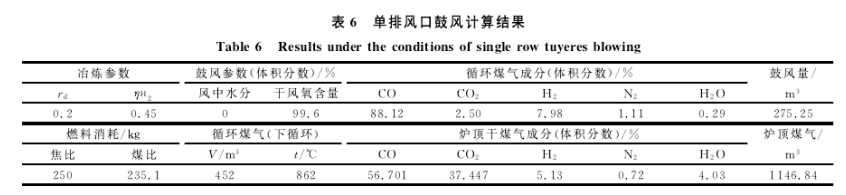
由表6可以看出,在和普通高爐相同碳素消耗的情況下,在直接還原度為0.2時,氧氣高爐需要補充噴吹脫除CO2至2.5%的循環(huán)煤氣452m3,且為滿足熱量需求,煤氣需被加熱到862℃,此時噸鐵煤氣量為1146.84m3,能夠輸出熱值為7707.82kJ/m3的煤氣444.37m3。與普通高爐相比,輸出煤氣總熱值減少1.05GJ,風口循環(huán)煤氣帶入的顯熱為0.445GJ。在扣除高爐自用加熱能量外,在輸出能量相同的情況下,全氧高爐節(jié)約能耗為1.8155-1.05-0.445=0.3205GJ,如果該部分能量價值大于噸鐵制氧的消耗+煤氣分離CO2。的消耗,則全氧高爐是節(jié)能的??紤]到普通高爐煤氣的能量利用效率并不是很高,因此減少輸出煤氣的總熱值從而返回高爐作為還原劑使用是有利的,因此全氧高爐降低燃耗措施主要是降低直接還原度、提高循環(huán)煤氣溫度以及減少凈輸出煤氣總熱值。此外可以看到,利用純氧鼓風,可以加大噴煤量,實現(xiàn)以煤代焦,這也可帶來可觀的經濟效益。
高爐使用雙排風口可以靈活地實現(xiàn)高爐溫度的上下部調節(jié),進而滿足高爐順行的要求。以最低燃料比、最大循環(huán)煤氣量、煤氣加熱不借助外來能源為目標,計算了雙排風口時高爐的能量利用情況,計算條件和單排風口時相同。由圖3的計算結果可知,最低燃料比為385.6kg/t,上風口循環(huán)煤氣量為480m3,下風口為379m3,煤氣溫度為983℃,不外供媒氣,除循環(huán)煤氣外,剩余煤氣全部用于加熱循環(huán)煤氣。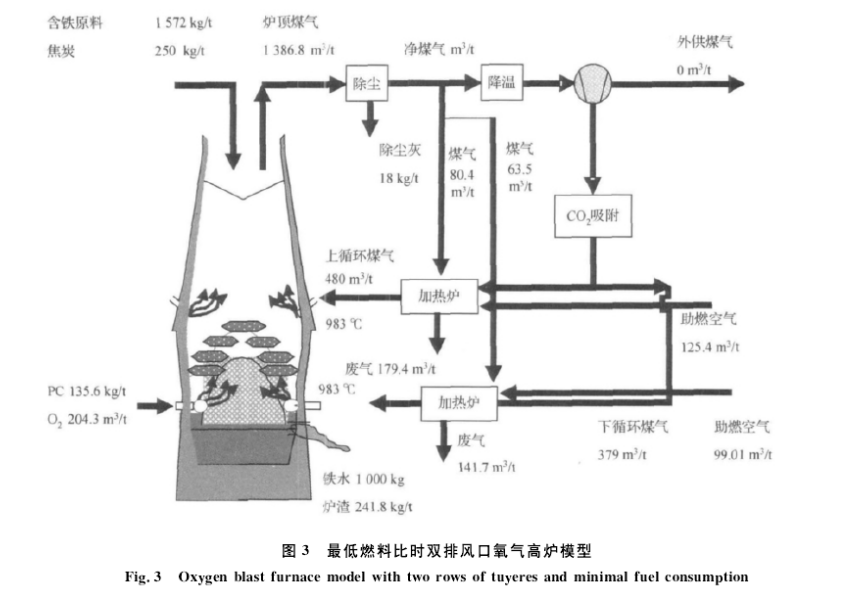
2.3噴吹焦爐煤氣
焦爐煤氣作為煉焦生產的副產品,富含大量的氫和甲烷,如表7所示。目前焦爐煤氣主要應用于普通加熱、燃氣發(fā)電、生產直接還原鐵和制氫,高爐噴吹焦爐煤氣在國內外業(yè)已開展過很多富有成效的研究。高爐噴吹焦爐煤氣主要是利用氫的間接還原降低直接還原度,從而達到節(jié)約碳消耗的目的。因此氫氣在高爐內的利用率成為限制其節(jié)碳效果的關鍵因素。此外由于氫氣的間接還原為吸熱反應,對熱量的需求增加。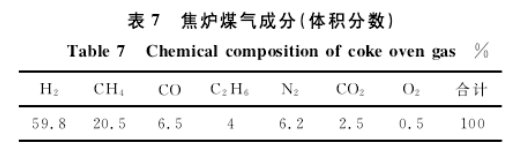
計算過程中直接還原度的確定采用前蘇聯(lián)拉姆教授總結的直接還原度經驗計算公式:
λ——表明噴吹物化學成分的系數(shù),如式(2)所示。


計算過程中保持煤比不變,固定熱損失為熱收入的5%,控制理論燃燒溫度在2000℃~2300℃。焦比與噴吹量和富氧率的關系如圖4所示。由圖4中看出,焦比隨噴吹量呈現(xiàn)先減小后增大的趨勢,這是由于在較低噴吹量階段,隨著噴吹量的增加,由于參加還原反應的氫氣量增加,直接還原度降低,碳耗降低;但同時,由于噴吹量增加,爐腹煤氣量增大,且焦爐煤氣的分解和溶損反應吸熱增加,風口前理論燃燒溫度逐漸降低,當噴吹量達到一定程度時,理論燃燒溫度低于最低2000℃的要求,則需要增加風口前燃燒的碳量以保證理論燃燒溫度因此焦比增加。對比不同富氧情況可見,隨著富氧率增大,對應最低焦比的噴吹量增大,最低焦比值減小,但減小速率逐漸降低,這是由于提高富氧率可以提高理論燃燒溫度,為保證理論燃燒溫度所需燃燒的碳量降低。在計算采用的原料條件下,當富氧率為6%~8%,噴吹量為160~180m3/t時,高爐焦比最低為266~267kg/t,比基準期320kg/t降低了53~54kg/t。
2.4應用高反應性焦炭
近年來,國內外冶金工作者開展了高爐使用高反應性焦炭的研究。通過使用高反應性焦炭降低碳素溶損反應起始溫度,進而降低間接還原平衡時CO分壓.從而達到提高煤氣利用率,降低燃料消耗的目的。鐵氧化物間接還原消耗的還原劑量是由FeO→Fe的還原反應決定的,根據(jù)高爐Rist操作線可知,如圖5所示。
W點為在還原溫度下間接還原,即通常認為的熱儲備區(qū)溫度1000℃,反應達到平衡時所能達到的最大O/C原子比值。高爐熱儲備區(qū)溫度由碳素溶損反應溫度決定,當碳素溶損反應溫度降低,比如從1000℃降到700℃時,則間接還原反應達到平衡時的O/C原子比增大,即W點向右移,煤氣利用率升高,直接還原度下降,直接還原耗熱減少,P點上移,燃料比下降。為考察使用高反應性焦炭的節(jié)能潛力,利用模型計算了不同CO平衡分壓時,高爐燃料比、直接還原度以及煤氣利用率的變化,計算過程中保持320kg/t的焦比不變,調整煤比,并假設間接還原反應均能達到平衡。計算結果如圖6所示。
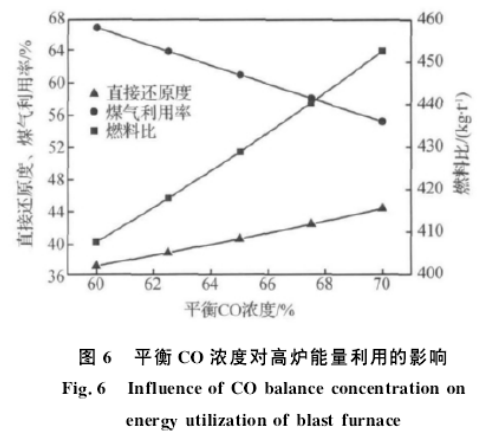
可以看出,隨著平衡時CO濃度的降低,煤氣利用率上升,燃料比下降,且下降速率高于直接還原度降低的速率。這是因為直接還原度降低,不但作為還原劑的碳素消耗減少,而且由于吸熱的直接還原反應量降低,高爐熱量需求降低,因此燃料比的下降速率要高于直接還原度降低的速率。CO平衡濃度從70%到60%每降低2.5%,節(jié)約燃料比分別為12.20、11.53、10.91、10.30kg/t。同時燃料比降低的前提是間接還原反應能夠達到平衡。根據(jù)還原反應動力學,一方面CO平衡濃度降低,在還原劑初始濃度不變時,還原的驅動力增大,還原速率增加;另一方面反應溫度降低,氣體擴散系數(shù)下降,化學反應速率常數(shù)下降,造成反應速率降低。若溫度對反應速率的影響大于平衡濃度的影響,將造成間接還原遠離平衡,爐身效率下降,反而會使直接還原度升高,造成燃料比上升。因此,為實現(xiàn)通過降低平衡時CO濃度的方法降低燃料比,需在使用高反應性焦炭的同時,努力提高爐料還原性。在高反應性焦炭方面,日本學者通過在煉焦配煤中使用高鈣煤達到了很好的效果,此外,也有利用鐵氧化和焦炭之間的鐵焦耦合反應來促進碳素溶損反應的報道。在提高爐料的還原性方面,國內外研究很多,值得注意的是,利用高反應性炭質如生物質焦和鐵礦粉混合壓塊來提高整體爐料的還原性正在成為研究的熱點。
3. 結論
(1)對于一般高爐而言,主要通過提高爐身效率降低燃料消耗,當間接還原達到平衡時煤氣利用率能夠達到56.99%,可降低燃料比28.37kg/t,折合23.09kg碳;提高煤氣利用率主要通過改善原料還原性以及控制合理煤氣流分布實現(xiàn)。(2)計算了全氧鼓風條件下不同煤氣循環(huán)方式的高爐能量利用情況。對于單排風口,在保持碳消耗量相同時需補充噴吹脫除CO至2.5%的循環(huán)煤氣452m3,且為滿足熱量需求,煤氣需被加熱到862℃。在雙排風口補充噴吹循環(huán)煤氣時,在爐頂煤氣完全循環(huán)利用條件下,燃料比最低可降到385.6kg/t。(3)噴吹焦爐煤氣可以降低燃料比,每增加10m3噴吹量,可降低焦比5.0kg/t左右;此外噴吹量存在極值,隨著富氧率提高,獲得最低燃料比的噴吹量增大,且最低燃料比降低。最佳噴吹條件為富氧率6%~8%,噴吹量160~180m3/t時,可節(jié)約焦比53~54kg/t。(4)使用高反應性焦炭可以降低熱儲備區(qū)溫度使問接還原平衡時CO濃度降低,平衡CO濃度從70%~60%,每降低2.5%,理論上可降低燃料消耗10.3~12.2kg/t,且降低幅度逐漸減小。
4. 參考文獻
[1] 徐國迪. 低碳經濟與鋼鐵工業(yè)[J], 鋼鐵, 2010, 45(3):1.
[2] 楊天鉤, 張建良, 左海濱. 節(jié)能減排 低碳煉鐵 實現(xiàn)中國高爐生產的科學發(fā)展[J], 中國冶金, 2010, 20(7):1.
[3] Ariyama Tatsuro, Sato Michitaka Optimization of Ironmaking Process for Reducing CO2 Emissions in the Integrated Steel Works[J]. ISIJ International, 2006,4612):1736.
[4] Zuo Guangqing, Hirsch Alexandra. The Trial of the Top Gas Recycling Blast Furnace at LKAB and Scale-up [C].//Proccedings of the 4th Ulcos Seminar Esscn: 2008.
[5] 齊淵洪,嚴定鎏,高建軍,等,氧氣高爐工業(yè)化試驗研究[J]鋼鐵,2011,46(3):7.
[6] Peter Diemer, Hans-Jurgen Killich, Klaus Knop, et al. Potentals for Utilization of Coke Oven Gas in Integrated Iron and Steel Works[J].Stahl und Eisen. 2004,124(7):21.
[7] 沙永志,曹軍,王風岐. 高爐噴吹焦爐煤氣[C]//第七屆(2009)中國鋼鐵年會論文集,北京:2009.
[8] Aramaki T. Status of the Coke Oven Gas in Japan[J].Journal of the Japan Institute of Energy, 2006.85(5):342.
[9] NOGAMI Hiroshi, YAGI Jun-ichiro, SAMPAIO Ronaldo Santos Energy Analysis of Charcoal Charging Operation of Blast Furnace[J].ISIJ international, 2004, 44(10):1646.
[10] ShimoyamaIzumi. Rescarch Prospect on Cokc Reactivty ai ming at Low RAR Blast Furnace Operation LI. Tetsuto Hagane.2010,96(5):209.
[11] 拉姆AH. 現(xiàn)代高爐過程的計算分析[M].王筱留, 譯.北京:治金工業(yè)出版社,1987.