長期以來,河鋼宣鋼2座2500m3高爐存在著壓差高、噴煤比低、焦比高、爐況穩(wěn)定性差的問題,尤其是高焦比、低噴煤比導致高爐經(jīng)濟技術指標與先進企業(yè)差距較大。經(jīng)過多次攻關調(diào)整,整體經(jīng)濟技術指標與爐況穩(wěn)定性得到一定改善,但仍不理想。
為突破技術瓶頸,河鋼宣鋼與河鋼鋼研和東北大學合作,針對煉鐵原燃料性能、高爐透氣性影響因素、堿金屬-焦炭的相互作用機理及規(guī)律等開展了全面研究,明確了影響指標提升的關鍵因素及其內(nèi)在聯(lián)系,找出了煤比難以提高的原因,為提高煤比指明了方向。
01
關鍵技術研究
通過試驗、數(shù)據(jù)分析及與行業(yè)內(nèi)其他高爐對比發(fā)現(xiàn),噴吹煤粉的基礎性能(如,化學成分、輸送性能、可磨性、燃燒性、爆炸性等),鐵料及配礦因素,并不是影響高爐指標提升的關鍵因素。同時還發(fā)現(xiàn)高爐堿金屬富集、焦炭熱性能及其與堿金屬的交互作用行為、高爐透氣性等因素是影響高爐噴煤比提高的關鍵;礦焦混裝及其方式對料柱透氣性影響顯著;并探究出一定堿負荷條件下焦比與煤比的對應關系。
1.1堿金屬來源及其影響
1.1.1堿金屬來源及負荷
原燃料中堿金屬含量如圖1~6所示。可以看出,河鋼宣鋼所用焦炭的堿金屬含量并不高,高爐中的堿金屬主要來自礦石和煤粉。由于堿金屬對高爐料柱透氣性及經(jīng)濟技術指標影響較大,要想保證高爐的透氣性,就必須降低礦石和煤粉的堿金屬帶入量。2018年下半年以前,河鋼宣鋼高爐堿負荷在行業(yè)中處于偏高水平。隨著對噴煤比影響因素的深入研究,逐步意識到改變原料條件、降低堿負荷的重要性和緊迫性。從2018年下半年起,逐步將堿負荷降低至2.0kg/tHM以下。
1.1.2焦炭熱性能及與堿金屬交互行為
焦炭反應性及反應后強度檢測結果如表1所示。
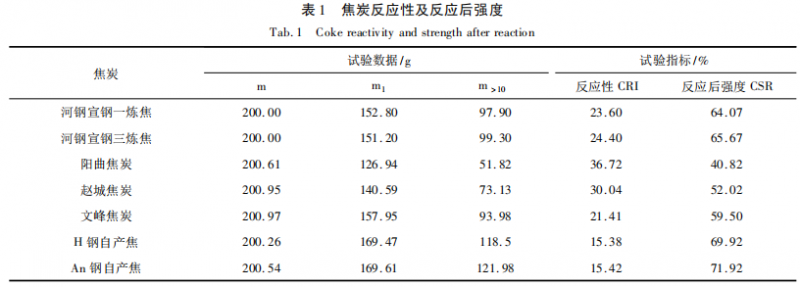
兩種自產(chǎn)焦性能比較穩(wěn)定,但與H鋼和An鋼(行業(yè)內(nèi)典型企業(yè))焦炭質(zhì)量相比仍有差距,這正是限制河鋼宣鋼提煤降焦的影響因素之一。外購焦整體質(zhì)量比自產(chǎn)焦差,不利于保證高爐透氣性和受風受煤能力。要想提煤降焦,需要提高入爐焦炭質(zhì)量,改善軟熔帶透氣性。
為考察堿金屬行為對焦炭熱性能的影響,對浸堿后焦炭的熱態(tài)性能進行了試驗。K2O含量及焦炭的熱態(tài)性能指標變化情況如表2所示。
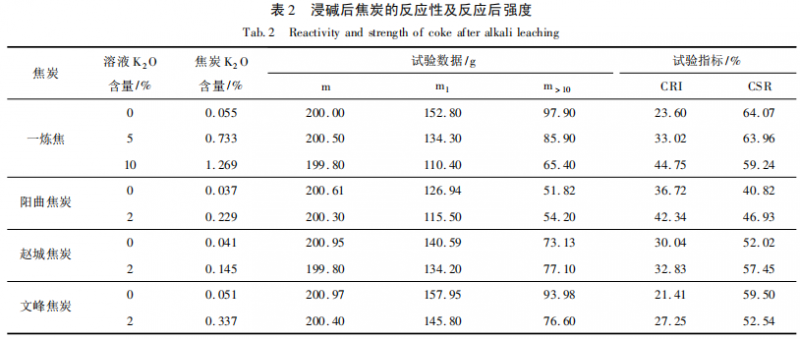
從試驗結果可以看出,質(zhì)量越好的焦炭,抗堿能力越差。因此,在提高焦炭質(zhì)量的情況下,一定要注意控制堿負荷,否則即使焦炭質(zhì)量提高了,噴煤比也難以提高,這也是該研究提出的提煤降焦的重要技術措施之一。
1.1.3浸堿后焦炭熱性能及與堿金屬交互行為
堿金屬是焦炭溶損反應的催化劑,隨著焦炭浸堿量的增加,焦炭反應性都明顯增加;CSR有降低,但也有的變化不大。其根本原因主要是焦炭與CO2發(fā)生的溶損反應屬于氣-固類非均相反應,是通過CO2和焦炭表面上活化點不斷反應來完成。目前,普遍接受的溶損反應過程機理是“內(nèi)擴散控制”和“界面反應控制”兩類。因此,CSR有降低也有變化不大的本質(zhì)原因由焦炭溶損反應的限制性環(huán)節(jié)決定的。
對于質(zhì)量較好的焦炭,溶損反應過程由“界面反應控制”。該過程為一級不可逆反應,氣化反應速率可由相界面反應或局部反應控制的Mckewan方程(1)表示。這種情況下CO2可以擴散至焦炭顆粒內(nèi)部,使得CO2在焦炭表面和內(nèi)部同時發(fā)生反應,從而破壞焦炭的內(nèi)部結構。堿金屬含量越高,對焦炭內(nèi)部結構的破壞越強,反應后強度CSR降低越明顯。
1-(1-R)1/3=kt(1)
式中,
R——反應半徑,cm;
K——反應常數(shù);
T——反應時間,min。
界面反應控制時反應體系CO2氣體濃度分布如圖7所示。
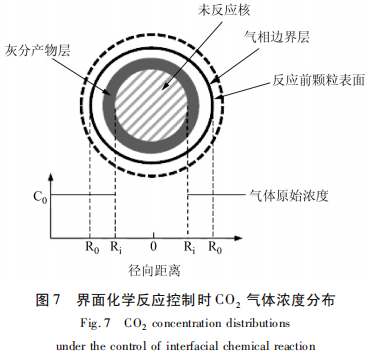
對于質(zhì)量較差的焦炭,如外進焦炭,溶損反應過程由“內(nèi)擴散控制”,該擴散過程符合菲克定律,反應速率可由Ginstling-Brounshtein方程(2)或者Jander方程(3)表示。這種情況下,由于焦炭本身溶損反應速度比較快,再加上堿金屬的催化作用,使得CO2難以擴散至焦炭顆粒內(nèi)部,對焦炭的內(nèi)部結構影響較小。因此,堿金屬含量越高,焦炭反應性越高,但反應主要發(fā)生在表面,對內(nèi)部結構破壞較小,而實驗過程中的高溫加熱對焦炭內(nèi)部結構又提供一次高溫結焦的作用(為提高產(chǎn)量和降低成本,焦炭生產(chǎn)過程中存在著結焦溫度或結焦時間不夠的現(xiàn)象,產(chǎn)生了部分質(zhì)量較差的生焦),因此質(zhì)量較差的焦炭浸堿后反應后強度CSR變化不大(略微升高)。
1-2/3R-(1-R)2/3=kt(2)
[1-(1-R)1/3]2=kt(3)
1.2礦焦混裝對料柱透氣性影響
及其加入方式
生產(chǎn)實踐證明,熔滴性能可準確反映軟熔帶透氣性的變化情況。
1.2.1熔滴性能分析
試驗加入的焦丁量按計算溶損反應碳消耗量的40%與礦石混合加入。熔滴試驗對比如圖8和表3所示。
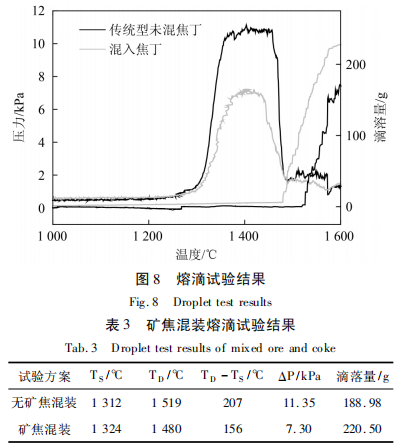
通過礦焦混裝,壓差降低了36%,說明礦焦混裝對于改善熔滴性能以及料柱透氣性效果明顯。由于焦炭混入燒結礦中,會發(fā)生碳的熔損反應,提高氣氛還原勢,F(xiàn)eO含量降低,渣的熔點提高,從而導致TS溫度上升。礦焦混裝的方式焦炭中的灰分會以SiO2形式進入初渣中,使得初渣堿度降低,使熔點初渣降低,而且液相量增加顯著,這是礦焦混裝TD降低的根本原因。
1.2.2混裝焦丁加入量的控制
焦丁的加入量由高爐直接還原度決定的,即有多少碳發(fā)生溶損反應。發(fā)生溶損反應的碳,來源于焦丁或大塊焦,其消耗量是固定的。沒有焦丁時,就與大塊焦反應。試驗證明,焦丁的加入量可取溶損反應碳量的0.4~0.7倍系數(shù),其余由未燃煤粉和大塊焦參加反應,這樣加入的焦丁不會影響焦窗透氣性。實際生產(chǎn)中需要結合生產(chǎn)數(shù)據(jù)定量分析。
1.2.3混裝焦丁加入粒度的控制
焦丁粒度不易太大,否則易造成分布不均,并在塊狀帶發(fā)生偏析。建議焦丁粒度下限為7~8mm(5mm篩子),上限為25mm,在進入軟熔帶前必須消耗掉,否則變成焦粉,初渣變粘。
1.3堿負荷-焦比-煤比關系
基于原燃料條件和生產(chǎn)大數(shù)據(jù)統(tǒng)計,得出焦比和煤比的關系式,用于計算一定堿負荷條件下對應的焦比與煤比。
焦比=堿負荷×0.0228+264.31(4)
煤比=堿負荷×(-0.027)+256.63(5)
02
技術措施
2.1控制堿金屬富集
河鋼宣鋼從控制含鐵原料和煤粉堿金屬含量入手,同時綜合考慮冶金性能降低堿負荷。通過一段時期控制,堿金屬富集得到了有效改善。近年來河鋼宣鋼高爐的堿金屬平衡分析如圖9所示。
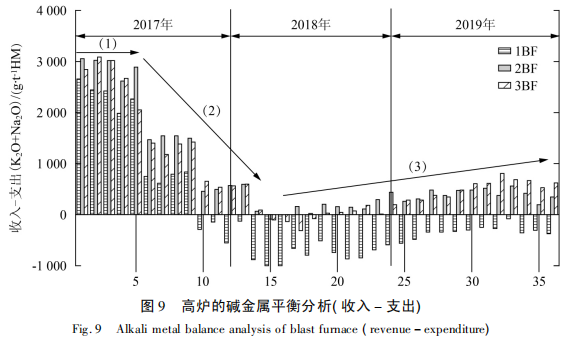
2.2焦炭高效利用
為了保證焦丁的加入量和大塊焦的粒度均勻性,設定焦丁粒度為8~25mm。生產(chǎn)中適當擴大焦炭入高爐篩孔的上限尺寸,將焦丁配比提高5~10kg/tHM。焦丁配入量增加及粒度變化使焦窗焦炭的尺寸區(qū)間變小,有利于焦炭整粒,提高焦窗焦炭的強度,保證軟熔帶焦窗的透氣性。
嚴格控制煉焦用煤的堿金屬含量,通過合理配煤提高焦炭熱性能并降低灰分,使得焦炭整體質(zhì)量有所提高,M40由84%提高至85%,反應后強度由63%提高到66%。
2.3基于堿負荷-焦比-煤比關系的
提煤降焦操作
以堿負荷-焦比-煤比關系為基礎,首先確定合理的焦比,再提高煤比。
2.4高爐操作
適當發(fā)展中心氣流,提高鼓風動能,吹透中心。階段性調(diào)整爐渣堿度,提高爐渣排堿能力應對堿負荷高對高爐的影響。
針對2018年以來風溫大幅度下降的現(xiàn)狀,通過提高爐腹煤氣指數(shù)和富氧率,保證鼓風帶入的熱量和煤粉的快速燃燒,減少不利影響。
03
實施效果
1號高爐煤比由135kg/tHM提高至175kg/tHM(2019年位列全國同級別高爐首位),2號高爐煤比由120kg/tHM提高至160kg/tHM,焦比降低約33kg/tHM,取得了良好的應用效果和經(jīng)濟效益、社會效益。1號、2號高爐熱風溫度降低50℃左右的情況下能耗指標變化趨勢如圖10所示。
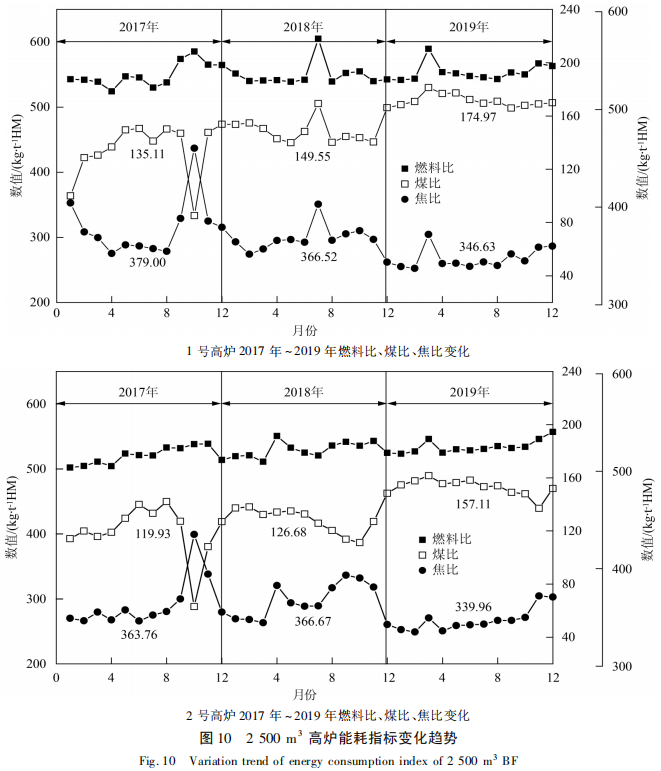
04
結論
(1)堿金屬對高爐爐況和指標提升影響巨大,必須嚴格控制其在煉鐵系統(tǒng)中的富集。
(2)堿金屬、煤粉、焦炭的交互行為在高爐中有規(guī)律可循,質(zhì)量越好的焦炭,抗堿能力越差。
(3)適當提高焦丁混裝比例,控制好焦丁粒度和加入方式可以有效提高高爐透氣性。