隨著我國能源消耗量的激增,過度依賴煤炭造成了嚴重空氣污染,大規(guī)模使用清潔能源天然氣已成為必然發(fā)展趨勢(國務(wù)院能源發(fā)展戰(zhàn)略行動計劃(2014-2020))。至2020年,我國天然氣表觀消費量將達4100億m3,其中需進口1400億m3,海上進口液化天然氣(LNG)占進口量的50%,將達700億m3,基于此,我國計劃建設(shè)超過200個特大型LNG儲罐、約60艘海上運輸船,LNG儲運設(shè)施的總投資近萬億人民幣,其中儲運設(shè)施關(guān)鍵材料鎳系低溫鋼的用量將高達60萬噸。日、韓兩國已開發(fā)出節(jié)鎳型LNG用鋼,LNG儲罐建造質(zhì)量提高、造價降低。而我國節(jié)鎳型LNG鋼尚屬空白,威脅著LNG儲運設(shè)施的自主建設(shè)及國際競爭力。我國液化天然氣(LNG)海上進口量至2020年可達700億m3/年,為此LNG儲罐用鋼需求總量將達60萬噸,急需新型鋼材以降低成本、提高儲罐質(zhì)量。在新型超低溫材料的開發(fā)中,高錳奧氏體鋼由于其價格、低熱膨脹系數(shù)和低周疲勞性能的顯著優(yōu)勢而備受關(guān)注。高錳奧氏體鋼采用錳和碳穩(wěn)定奧氏體相,在室溫條件下獲得單相奧氏體組織,而奧氏體鋼一般不存在韌脆轉(zhuǎn)變現(xiàn)象,因此高錳奧氏體鋼具備超低溫(-196℃)應(yīng)用的先天優(yōu)勢。另外,隨著現(xiàn)代社會的發(fā)展,人類對能源的需求也日益增多。在清潔能源領(lǐng)域,可控核聚變的主要燃料為氫的同位素,可從海水中獲取,具有儲量豐富、效率高的特點,有望成為解決人類能源匱乏的有效途徑。然而,核聚變裝置—全超導(dǎo)托卡馬克(EAST,俗稱“人造太陽”)在工作時會產(chǎn)生巨大的電流,為降低電流的熱效應(yīng)對核聚變系統(tǒng)的不良影響,低溫超導(dǎo)技術(shù)成為發(fā)展可控核聚變的必然選擇。這需要將全超導(dǎo)托卡馬克裝置的中央超導(dǎo)磁體置于4.2K的環(huán)境下以實現(xiàn)超導(dǎo)特性,極端的服役環(huán)境和核聚變裝置的安全性對包裹超導(dǎo)磁體的結(jié)構(gòu)材料提出了近乎苛刻的要求,需要在4.2K下具備無磁、高強韌性等優(yōu)良性能。此外,為配合Nb3Sn超導(dǎo)磁體的制備過程,包裹超導(dǎo)磁體的結(jié)構(gòu)材料需在室溫進行一定的預(yù)變形后在650℃左右進行長時間(約200h)的時效處理以達到最優(yōu)的超導(dǎo)性能,這對結(jié)構(gòu)材料的抗時效脆性也有著嚴格的要求。長期以來,此類極低溫條件下多使用316LN型、304型不銹鋼等材料,日本原子能廳和神戶制鋼近期也開發(fā)了JK2LB不銹鋼,但是上述幾類不銹鋼需要添加大量的Cr、Ni、Mo等貴重金屬,一方面會導(dǎo)致嚴重的敏化脆性問題,影響極低溫使用性能;另一方面,大量貴重金屬的使用也造成了成本、資源的消耗。因此開發(fā)新型的極低溫(4.2K)用無磁材料成為發(fā)展的必然趨勢。但是高錳鋼由于其面心立方晶體結(jié)構(gòu)的特征,導(dǎo)致其屈服強度相對較低(通常在200~400MPa之間),使其在工程應(yīng)用方面具有一定的局限性,亟待解決LNG儲罐用熱軋高錳鋼屈服強度低這一問題。目前,主要采用固溶強化、細晶強化和沉淀強化等方式來提高屈服強度,但對于具有面心立方晶體結(jié)構(gòu)的高錳鋼,固溶原子的固溶強化效果遠低于其在體心立方晶體結(jié)構(gòu)鐵合金中的固溶強化效果。細化晶??梢杂行У靥岣咔姸?,但是,只有將晶粒細化至5μm以下時,實驗鋼的屈服強度接近400MPa,另外,高錳鋼通常在500~800℃進行退火處理,以獲得再結(jié)晶細化組織,當退火溫度高于800℃時,組織發(fā)生明顯的粗化。但我們的研究發(fā)現(xiàn),一方面高錳鋼存在一個500~800℃的脆性區(qū)間,另一方面高錳鋼的超低溫韌性隨著晶粒尺寸的減小而惡化,可見,采用充分細化晶粒來改善熱軋高錳鋼的屈服強度難以滿足其對超低溫韌性的苛刻要求。因此,在不顯著損害熱軋高錳鋼超低溫韌性的條件下,引入適當?shù)膹娀瘷C制成為亟待攻克的難題。二、解決問題的思路或技術(shù)原理(包括彩色示意圖)針對高錳奧氏體鋼固有的屈服強度低、強化和低溫韌性化相互矛盾以及力學(xué)性能各向異性的問題,首先基于層錯能開展合金化設(shè)計,建立強韌性與合金成分的關(guān)系,其次利用晶粒適度細化和微硬化進一步改善高錳奧氏體鋼的強度,最后利用夾雜物和軋制工藝改善各向異性,相關(guān)技術(shù)思路如圖1所示。
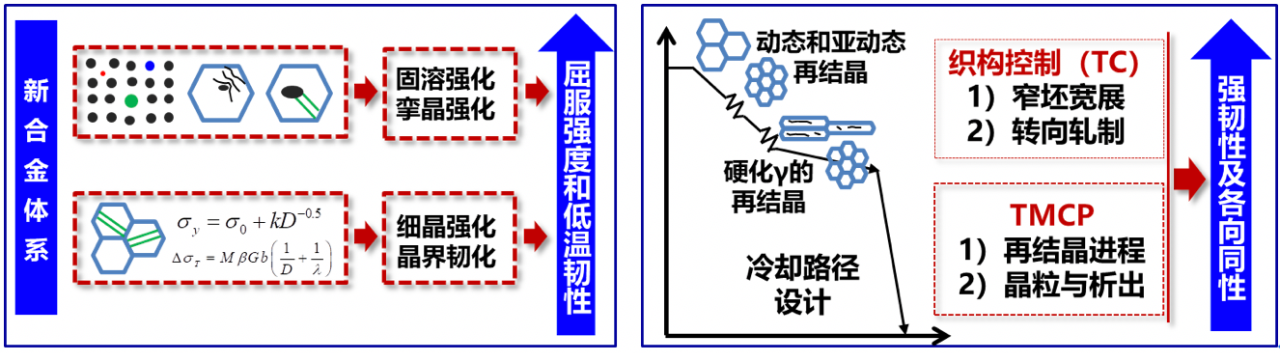
圖1 基于強韌性控制的合金化設(shè)計及工藝控制思路
1、基于SFE和屈服強度的合金化設(shè)計原理
基于高錳鋼面心立方晶體結(jié)構(gòu)的特點及焊接性能和超低溫服役性能的苛刻要求,提出了優(yōu)化的合金體系及“高溫軋制+超快冷”的短流程生產(chǎn)工藝,獲得再結(jié)晶組織,解決了高錳鋼所面臨的強度問題。系統(tǒng)研究了合金成分、TMCP工藝對高錳鋼力學(xué)性能的影響規(guī)律,如圖2所示。提出了新的高錳LNG儲罐用鋼合金設(shè)計(Fe-Mn-C-Cr-Cu-Nb/V/Ti和Fe-Mn-C-Al-Nb/V/Ti),在“高溫軋制+超快冷”短流程工藝條件下,在實驗室制備出YS>430MPa、TS>850MPa、KV2(-196℃)在135~160J的原型鋼,經(jīng)熱處理后,屈服強度可進一步提高至500MPa,為積極推進工業(yè)化試制及示范儲罐的建造奠定了堅實的理論基礎(chǔ)。另外,采用層錯能熱力學(xué)計算模型,計算了不同成分實驗鋼的層錯能,建立了層錯能與超低溫韌性間的關(guān)系,如圖3所示,可見將層錯能控制在38~44mJ/m2的范圍內(nèi),一般可獲得優(yōu)異的超低溫韌性,為高錳LNG儲罐用鋼的合金化設(shè)計提供了理論依據(jù)。
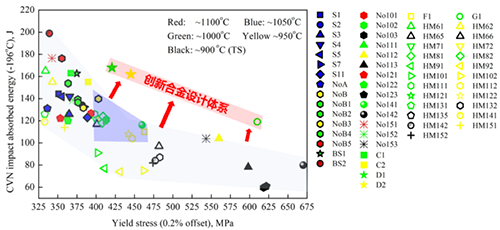
圖2 合金成分和工藝對高錳鋼屈服強度和超低溫韌性的影響
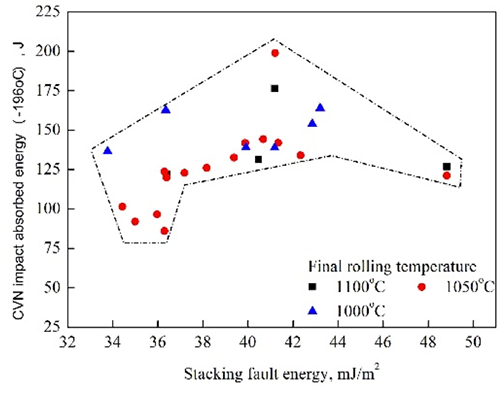
圖3 SFE對高錳奧氏體鋼-196℃沖擊韌性的影響
2、超低溫沖擊韌性的“反尺寸效應(yīng)”
不同再結(jié)晶區(qū)軋制溫度下實驗鋼的EBSD分析結(jié)果如圖4所示,圖中黑色線為一般大角晶界(取向差>15o)和Σ3退火孿晶界(取向差為60o)。不同終軋溫度下實驗鋼的顯微組織均為再結(jié)晶等軸組織,晶粒內(nèi)部存在較大尺寸的孿晶,隨著終軋溫度由1083℃降低至966℃,晶粒得的顯著細化。割線法測定了不同終軋溫度條件下的晶粒尺寸,結(jié)果顯示966℃、1000℃和1083℃終軋溫度下的平均晶粒尺寸(包括孿晶)分別為8.5μm、11.6μm和17.3μm。說明終軋溫度在966℃以上時,可通過反復(fù)動態(tài)再結(jié)晶或亞動態(tài)再結(jié)晶細化組織,終軋溫度顯著影響晶粒尺寸。
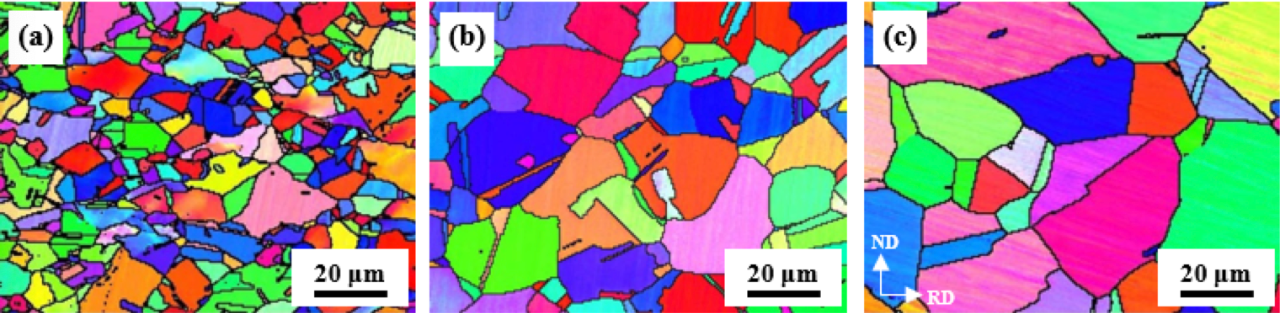
終軋溫度:(a)966℃;(b)1000℃;(c)1083℃不同終軋溫度下實驗鋼的工程應(yīng)力-應(yīng)變曲線如圖5示。不同終軋溫度下實驗鋼的工程應(yīng)力-應(yīng)變曲線均呈連續(xù)屈服現(xiàn)象,同時均具有良好的塑性。隨終軋溫度的降低,實驗鋼強度提高,組織的細化具有改善實驗鋼強度的作用,但即使在晶粒尺寸約為8μm時,實驗鋼的屈服強度僅有395MPa。圖6示出了屈服強度和晶粒尺寸間的關(guān)系,可見固溶強化和位錯強化對屈服強度的貢獻達到了260MPa。
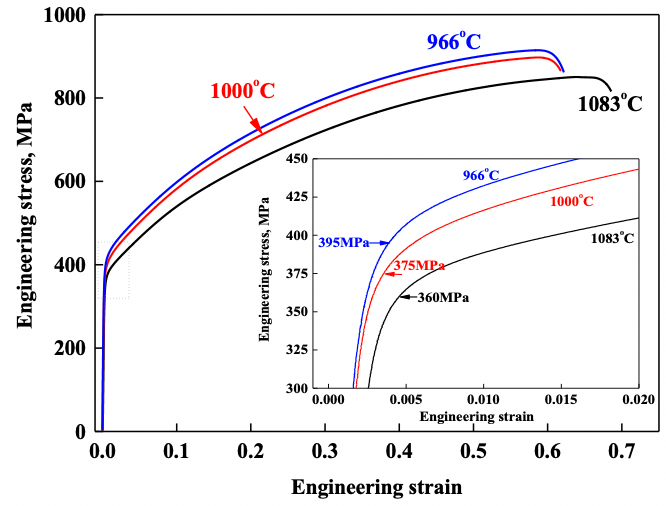
圖5 不同終軋溫度下實驗鋼的工程應(yīng)力-應(yīng)變曲線不同終軋溫度下實驗鋼的-196℃夏比沖擊吸收功如圖7所示。隨著終軋溫度的降低,晶粒尺寸得到顯著細化,但-196℃夏比沖擊吸收功不但沒有提高,反而出現(xiàn)明顯的下降趨勢,即晶粒尺寸越大,實驗鋼的超低溫韌性越好。同時,三種實驗鋼的沖擊斷裂均為塑性斷裂模式,隨著終軋溫度的升高,韌窩的尺寸和深度都顯著增加。

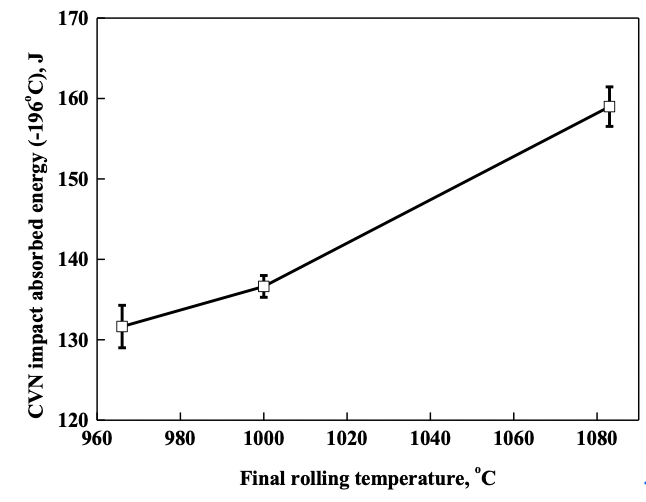
3、高錳LNG儲罐用鋼的熱處理脆性
基于熱處理工藝實驗研究,弄清了熱處理工藝對高錳鋼超低溫韌性的影響規(guī)律及機理,發(fā)現(xiàn)高錳鋼普遍存在一個時效脆性區(qū)間的共性問題,如圖8所示,并弄清了產(chǎn)生時效脆性的關(guān)鍵因素,提出了高錳LNG儲罐用鋼的高溫熱處理工藝。研究發(fā)現(xiàn),不同合金體系的高錳LNG儲罐用鋼均存在一個脆性區(qū)間的共性問題,時效脆性溫度區(qū)間為500~900℃。在150~500℃熱處理溫度范圍內(nèi),實驗鋼的超低溫沖擊吸收功基本保持不變,當熱處理溫度高于500℃時,超低溫沖擊吸收功出現(xiàn)急劇下降現(xiàn)象。900℃之后,隨著熱處理溫度的升高,低溫韌性又得到了的改善,此階段,韌性對溫度的變化很敏感,在1000℃時沖擊功達到了180J,相對于熱軋態(tài)提高了50J。1000℃之后,低溫韌性逐漸趨于穩(wěn)定,但仍以較緩的趨勢繼續(xù)增長。
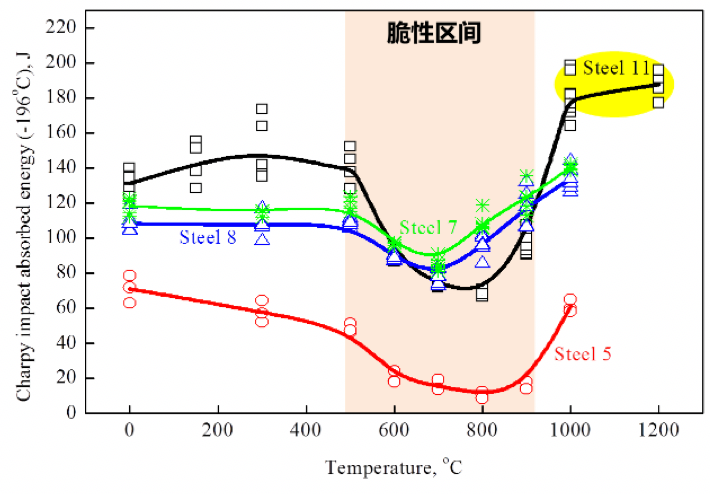
對300℃(300A)和800℃(800A)熱處理試樣進行深入分析。HADDF(High-Angle Annular Dark-Field)-STEM(Scanning Transmission Electron Microscopy)和EDX(Energy Dispersive X-ray)分析結(jié)果如圖9所示。圖9(a)顯示,在一般晶界處存在一定的元素偏聚現(xiàn)象,晶界是一種結(jié)構(gòu)缺陷,其自由能高于晶粒內(nèi)部的自由能,因此為了降低系統(tǒng)總的自由能,晶界同其他缺陷,如位錯、外部原子等,發(fā)生相互作用,這種相互作用將使外部原子向晶界偏聚。當熱處理溫度升高至800℃時,除了晶界偏聚,晶界處還分布有一定量的析出相,這些析出相富集Cr、Mn和C,且SAEDP(Selected Area Electron Diffraction Pattern)顯示這些析出相為(Cr,Mn)23C6型碳化物。圖10示出了晶界處的元素偏聚情況,對于300A實驗鋼,雖然晶界呈亮襯度,存在一定的元素偏聚,但EDX-STEM結(jié)果顯示,在晶界處未觀察到C、Cr和Mn的峰,但對于800A實驗鋼,在晶界處觀察到了Cr或C峰,表明800A實驗鋼的晶界偏聚程度大于300A實驗鋼??梢?,引起脆性的主要原因為晶界偏聚和嚴重的晶界析出。
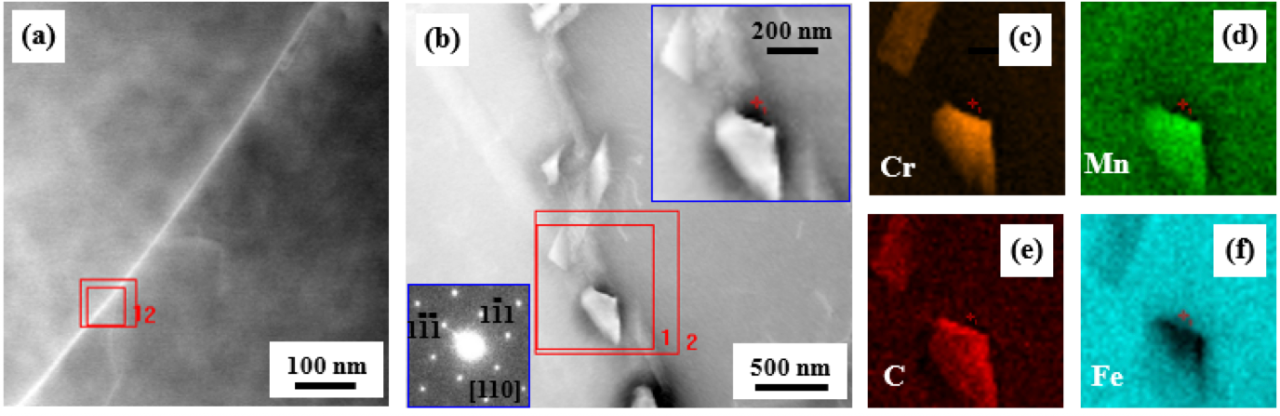
(c)(d)(e)(f)分別為圖b紅色方框區(qū)域的Cr、Mn、C和Fe分布圖

圖10 HAADF-STEM圖和與之對應(yīng)化學(xué)元素分布圖
4、基于非均質(zhì)組織的高錳奧氏體鋼強化
在高錳鋼可以大大提高鋼材的強度的同時也能保證其具有較高的超低溫沖擊韌性,通過這種硬化組織和再結(jié)晶組織的協(xié)同作用,良好的強度、韌性匹配可以在高錳奧氏體鋼中實現(xiàn),從而為低溫用高錳奧氏體鋼的開發(fā)提供一定的借鑒。圖11顯示,隨著再結(jié)晶退火程度的提高,組織中的硬化組織逐漸減少,小角度晶界的比例也隨之減少。同時,晶粒由壓扁狀的高能態(tài)逐漸轉(zhuǎn)變?yōu)榈容S狀的低能態(tài)奧氏體,奧氏體晶界也由崎嶇蜿蜒的形貌轉(zhuǎn)變?yōu)槠交瑘A潤的形態(tài),這也代表晶粒內(nèi)部的畸變能降低。從局部取向差分布圖(KAM)來看,奧氏體晶粒內(nèi)部的取向差也逐漸減少。軋態(tài)組織中約還有91%的硬相組織,而900℃退火10min(900A)后硬相組織降低至24%,而950℃退火(950A)后奧氏體晶粒發(fā)生了完全再結(jié)晶,硬相組織基本消失。同時從晶粒尺寸上看,900℃退火10min后晶粒尺寸較軋態(tài)的變化不大,由3.4μm轉(zhuǎn)變?yōu)?.2μm,而950℃退火10min后,伴隨著再結(jié)晶程度的提高,晶粒尺寸也略有長大,轉(zhuǎn)變?yōu)?.6μm。

IPF:(a)HR;(b)900℃×10min;(c)950℃×10min;KAM:a)HR;(b)900℃×10min;(c)950℃×10min;從圖12可以看出,退火后實驗鋼強度有一定程度的下降,但是塑性卻有較大的提高。900℃退火10min后得到最佳的強韌性匹配,它的超低溫韌性較完全再結(jié)晶態(tài)實驗鋼(950℃退火10min)僅下降17J,屈服強度卻提高近100MPa,抗拉強度提高近60MPa。進一步分析其原因,發(fā)現(xiàn)在應(yīng)變硬化曲線的stage Ⅱ階段,即塑性變形的初始階段,900A實驗鋼保持相對較高的應(yīng)變硬化能力,這主要與900A實驗鋼中由部分回復(fù)的硬化奧氏體組織和再結(jié)晶的軟化奧氏體組織組成的這種非均質(zhì)的結(jié)構(gòu)造成的。變形過程中在硬相和軟相之間會形成較多的幾何必須位錯,造成很強的背應(yīng)力強化效應(yīng),提高了軟相的強度,而在沖擊載荷下,軟相又能通過TWIP效應(yīng)和位錯滑移協(xié)調(diào)更多的變形,這也是900A實驗鋼同時具有較高強度和超低溫韌性的原因。
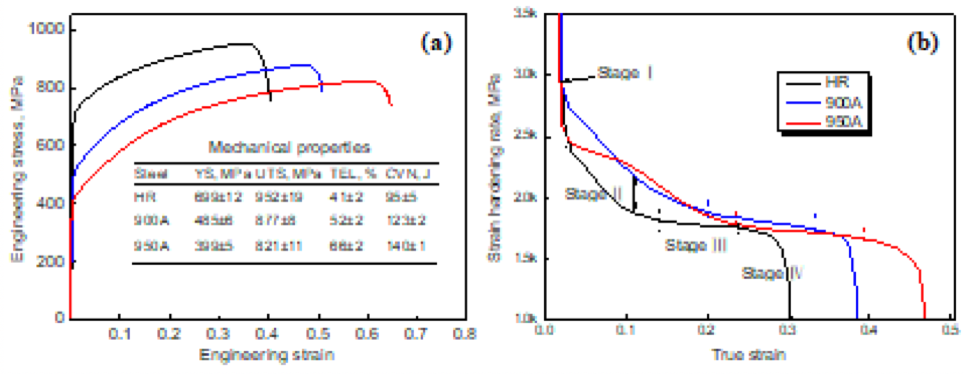
(a)工程應(yīng)力-應(yīng)變曲線及力學(xué)性能;(b)應(yīng)變硬化曲線
5、高錳奧氏體鋼的各向異性調(diào)控
在常規(guī)鑄錠-鍛造-軋制工藝條件下,高錳LNG儲罐用鋼的超低溫韌性呈顯著的各向異性,橫縱向的超低溫沖擊吸收功差值高達90J,如圖13(a)所示。為解決這一問題,采用連鑄坯-高溫轉(zhuǎn)鋼軋制工藝,顯著改善了超低溫沖擊韌性的各向異性,并且將此工藝應(yīng)用于不同成分體系的高錳LNG儲罐用鋼,發(fā)現(xiàn)此工藝均可以改善超低溫沖擊韌性的各向異性,不同強度級別實驗鋼的橫向和縱向沖擊吸收功差值在15~30J之間,如圖13(b)所示。

圖13 原工藝及新工藝條件下實驗鋼超低溫沖擊韌性的各向異性(a)原工藝和新工藝條件下沖擊韌性各向異性的比較;
6、高錳奧氏體鋼的各向異性調(diào)控
開發(fā)出應(yīng)用于4.2K超導(dǎo)領(lǐng)域的高錳極低溫用鋼,性能上兼具316LN和JK2LB(日本最近開發(fā)的高錳型不銹鋼)的優(yōu)勢,合金成本僅為前兩者的1/5。基于拉伸性能和斷裂韌性協(xié)同優(yōu)化設(shè)計,明確了綜合性能最佳的組織特征為高鋁鋼的大晶粒組織;所開發(fā)的高錳鋼兼具316LN的高斷裂韌性和JK2LB的高屈服優(yōu)勢(YS=1117MPa,UTS=1480MPa,TEL=34.2%,KIC=255MPa√m)。
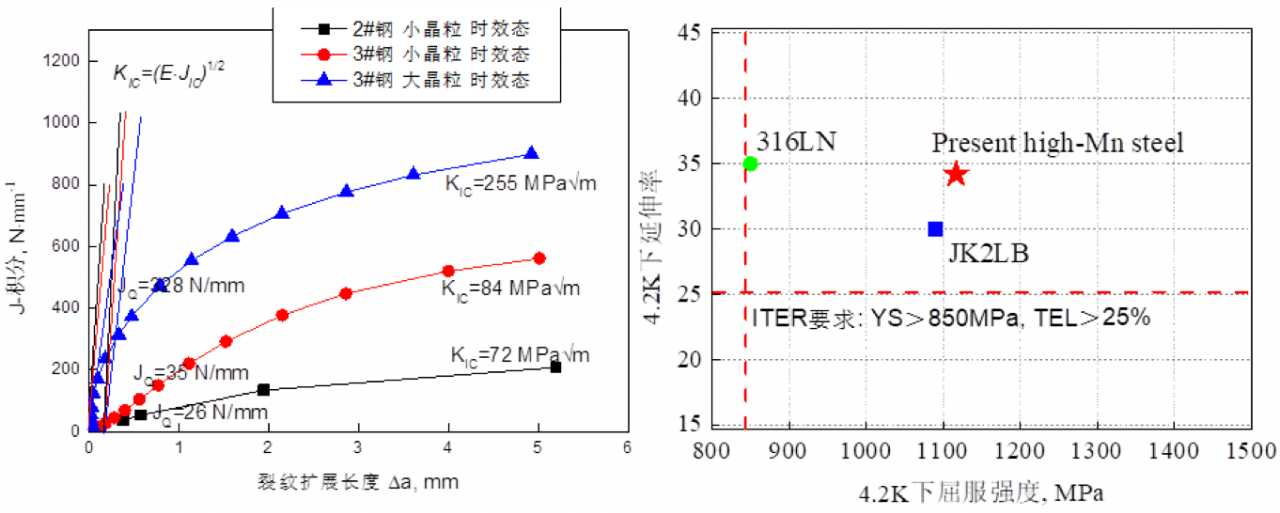
圖14 實驗鋼與316LN和JK2LB材料時效態(tài)樣品拉伸性能與斷裂韌性對比四、應(yīng)用情況與效果(包括有關(guān)效果對比說明圖、照片)山西太鋼不銹鋼股份有限公司、鞍鋼股份有限公司、南京鋼鐵股份有限公司和首鋼集團有限公司攻克連鑄關(guān)鍵難題,在國內(nèi)成功實現(xiàn)高錳LNG儲罐用鋼的連鑄生產(chǎn),經(jīng)探傷和低倍檢測,無偏析、裂紋、分層缺陷,連鑄坯實物質(zhì)量良好。并實現(xiàn)高錳鋼的工業(yè)化軋制,實物照片如圖15所示。試制鋼板屈服強度>400MPa,-196℃橫向沖擊吸收功>110J,并開發(fā)出LNG儲罐用高錳鋼專有焊材和焊接工藝。

在項目執(zhí)行過程中,東北大學(xué)大學(xué)牽頭起草《低溫壓力容器用高錳鋼鋼板》,目前已經(jīng)完成國家標準征求意見,于2021年6月16日審定標準最終稿,并列入《承壓設(shè)備用鋼板和鋼帶 第5部分:規(guī)定低溫性能的高錳鋼》,如圖16所示。
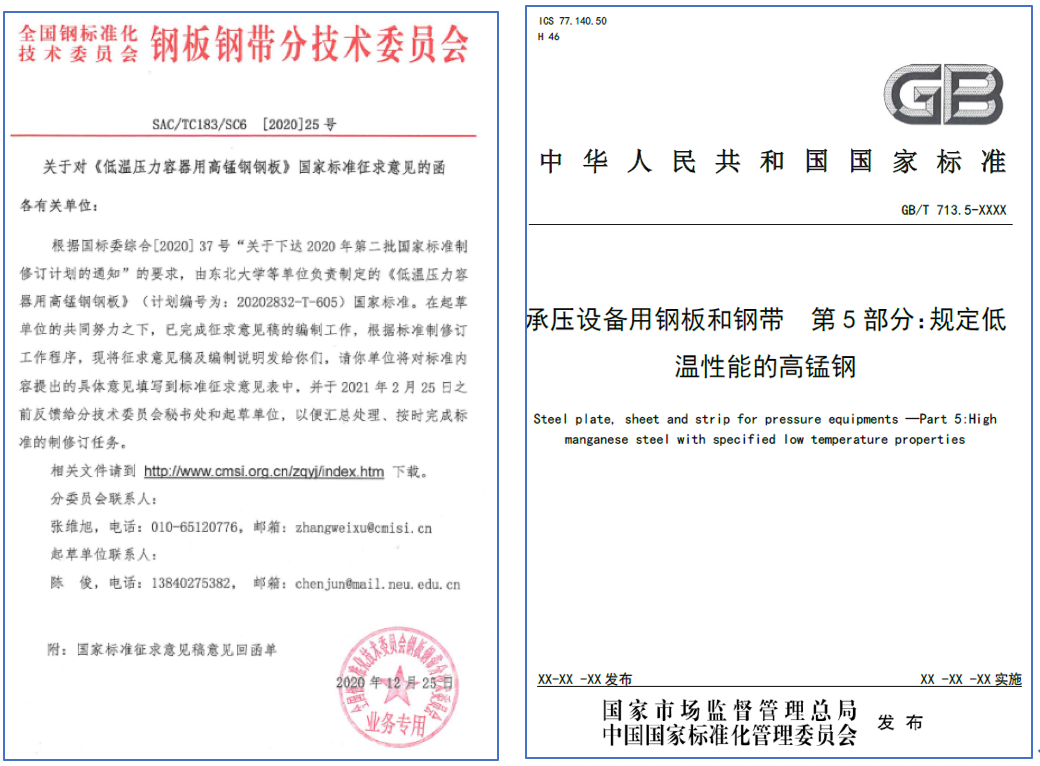
圖16 高錳鋼國家標準征求意見稿和承壓設(shè)備用鋼板和鋼帶中關(guān)于高錳鋼的標準采用鞍鋼股份有限公司生產(chǎn)的6mm和8mm高錳鋼鋼板,制造了5m3的小型試驗罐,如圖17所示。
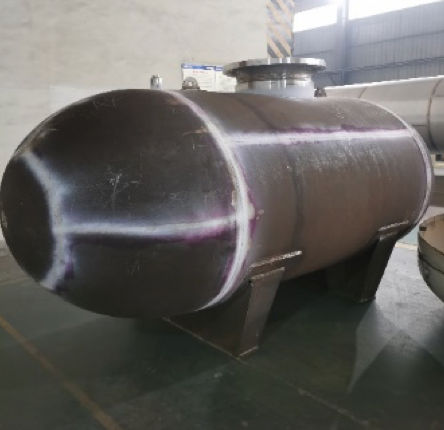