在煉鋼電爐冶煉的過程中,要產生大量的高溫煙氣,其最高溫度可達2000℃,且煙氣含塵量高。高溫含塵煙氣攜帶的熱量約為電爐輸入總能量高達20%。這些高溫煙氣不僅帶走大量的熱,而且給電爐的除塵系統(tǒng)帶來了巨大的負擔,不但降低了氧化鐵塵的回收率,而且造成了嚴重的污染問題。目前國內和國際上的電弧爐仍有很多沒有回收煙氣余熱,有的只是部分回收了煙氣余熱,隨著兌鐵水比例的增加,電弧爐煙氣的溫度變得更高。若不回收四孔煙氣的全部余熱,將會造成大量的能源浪費。隨著鋼鐵行業(yè)的發(fā)展,電爐煉鋼比例逐漸上升,電爐煉鋼煙氣余熱浪費和除塵問題日趨嚴重。如何將這部分高溫煙氣中的顯熱充分地回收,變“廢”為寶,并使得電爐煙氣更加穩(wěn)定,為高效除塵創(chuàng)造條件,從而降低除塵系統(tǒng)運行成本和企業(yè)的生產成本,這是電爐煉鋼企業(yè)必須重視的問題。中冶賽迪研發(fā)的電爐煙氣全余熱回收裝置見圖1。該裝置采用高低壓復合循環(huán)的冷卻方式,Ⅰ段煙道、燃燒沉降室頂蓋、Ⅱ段煙道、列管余熱鍋爐均采用汽化冷卻方式( 指與水進行換熱,使水汽化,從而煙氣降溫) 回收電弧爐四孔煙氣約220~2000℃的全部余熱,具有顯著的節(jié)能效果。
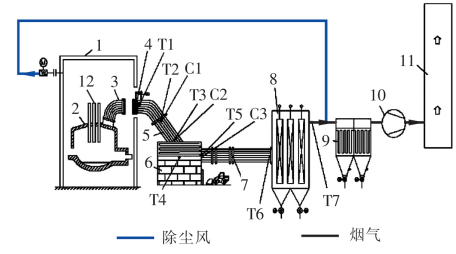
1-密閉罩 2-電弧爐 3-水冷彎頭 4-水冷滑套 5-Ⅰ段煙道6-燃燒沉降室 7-Ⅱ段煙道 8-列管余熱鍋爐 9-布袋除塵器10-風機 11-煙囪 12-電極 煙氣從電弧爐抽出后,與從水冷彎頭和水冷滑套間環(huán)縫混入的空氣一起進入Ⅰ段煙道,在Ⅰ段煙道內,煙氣降溫后進入燃燒沉降室。燃燒沉降室頂蓋采用了汽化冷卻結構,下半部分采用混凝土和耐火材料。燃燒沉降室設計的目的是,在燃燒沉降室內,煙氣中的CO燃盡,同時煙氣攜帶的粉塵粗顆粒也經重力除塵沉降下來。其后煙氣進入Ⅱ段煙道進行換熱,進一步降溫后進入列管余熱鍋爐,降溫至220 ℃ 以下后與密閉罩出口的除塵風混合送入布袋除塵器,除塵達標后的煙氣經過風機從煙囪排出。從圖1可以看出,電爐煙氣全余熱回收裝置從水冷滑套開始到列管式余熱鍋爐,回收電爐第四孔出口煙氣約2000~220℃的全部余熱。同時該裝置采用高低壓復合循環(huán)的冷卻方式,充分回收電爐煙氣余熱的同時,采用自然循環(huán)的列管式余熱鍋爐,與水冷系統(tǒng)相比,循環(huán)水量顯著減小,節(jié)約了電能。電爐煙氣全余熱回收裝置根據燃燒沉降室出口的煙氣成分,合理控制水冷滑套的開度,確保了最佳的過??諝庀禂?shù)。電爐煙氣中含有一定濃度的 CO,由于 CO 含量低于煤氣回收下限,一般采用二次燃燒技術回收一氧化碳的潛熱,而不進行煤氣回收。盡管目前國內出現(xiàn)了電爐大量兌鐵水,CO 濃度顯著增加的現(xiàn)象,但電爐的優(yōu)勢主要體現(xiàn)在短流程煉鋼,因此 CO 進行燃燒而不直接回收煤氣的工藝不會改變,在這種條件下,合理控制電爐余熱鍋爐系統(tǒng)混風量,既要保證 CO 的燃盡又要保持余熱鍋爐盡量高的熱效率就顯得尤為重要。

電爐冶煉過程中,參與爐氣燃燒的氧氣主要來源由3部分組成: 1) 吹氧冶煉爐氣中本身含有氧氣,2)從電爐的觀察孔、電極孔等漏入的空氣,3)為了保證爐氣中的CO全部燃盡從水冷滑套進入的空氣。因此根據燃燒沉降室出口煙氣成分控制水冷滑套混入的空氣量,通過壓力分析就能控制風機轉速來獲取最佳的過??諝庀禂?shù),使得余熱回收系統(tǒng)及除塵系統(tǒng)更加節(jié)能。電爐煙氣全余熱回收裝置另一個突出優(yōu)勢是高效沉降。中冶賽迪根據電爐煙氣粉塵濃度和粉塵粒徑,及粉塵的沉降機理,進行了數(shù)值模擬,開發(fā)了高效燃燒沉降室。燃燒沉降室的作用主要有三個:2)促進煙氣與空氣的混合,保證 CO等可燃成分的燃盡;3)對電爐煙氣進行粗除塵,減少進入余熱鍋爐煙道的煙塵量,保證余熱鍋爐的換熱效率和使用壽命。
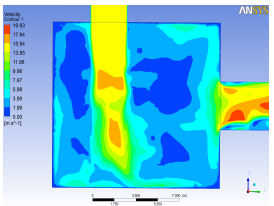
煙塵的有效沉降可以保障后續(xù)對流受熱面余熱鍋爐的換熱效率,同時減少了煙氣對鍋爐壁面的磨損,因此實現(xiàn)燃燒沉降室內煙塵的有效沉降是非常重要的。經過對燃燒沉降室內粉塵沉降的機理研究,電爐煙氣全余熱回收裝置采用直角式的燃燒沉降室,即煙氣從燃燒沉降室頂部進入,然后從側向流出的形式。同時根據模擬分析確定了合理的燃燒沉降室流通截面,確?;覊m的高效沉降。為了避免熱管換熱管在高溫煙氣條件下失效問題,中冶賽迪電爐煙氣全余熱回收裝置采用了列管式余熱鍋爐。列管式余熱鍋爐采用自然循環(huán),吹灰裝置采用激波吹灰,不僅提高對流受熱面余熱鍋爐的壽命,延長鍋爐換熱失效時間,而且提高汽包出口蒸汽壓力,便于蒸汽的利用。中冶賽迪開發(fā)的電爐煙氣全余熱鍋爐系統(tǒng)已經在江蘇省聯(lián)峰能源裝備有限公司新建110t電爐工程中進行工程利用,見圖4和圖5。
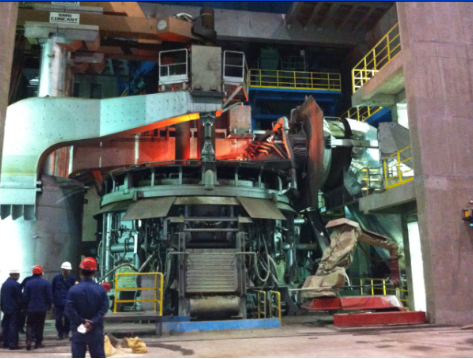
圖4 永鋼110t電爐余熱鍋爐(水冷滑套和彎頭煙道)
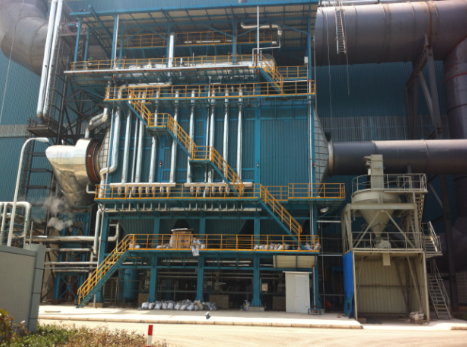
圖5 永鋼110t電爐余熱鍋爐(尾部煙道和列管式余熱鍋爐)汽化冷卻和水冷卻相比,本工程采用汽化冷卻系統(tǒng),不再建設水冷系統(tǒng)等設施,節(jié)省了工程用地,運行時,不再需要循環(huán)水泵、冷卻塔、機力風冷機等設備,降低了運行過程的能耗。經實際運行監(jiān)測,在電爐煉鋼達到設計參數(shù)時,本系統(tǒng)利用電爐冶煉的煙氣余熱,可產生壓力為1.8MPa的飽和蒸汽20t/h,折噸鋼蒸汽量約160kg/噸鋼。年節(jié)約標煤約0.72萬噸、減排CO2 1.63萬噸、減排SO2 144噸,減排灰塵0.2萬噸,環(huán)保十分效益顯著。