隨著國內(nèi)鋼鐵工業(yè)供給側(cè)改革、產(chǎn)業(yè)結(jié)構(gòu)調(diào)整、國標升級等政策的實施,線材行業(yè)向高品質(zhì)、低能耗、綠色化發(fā)展的步伐不斷加快。但長期以來受工藝技術及裝備水平等影響,國內(nèi)線材高速軋機裝備技術在提高產(chǎn)品品質(zhì)、降低軋制能耗及降低生產(chǎn)成本等方面進步緩慢。主要體現(xiàn)在:1)軋制能力小,不能適應低溫軋制。2)軋機剛性差,產(chǎn)品尺寸波動大。3)受制于傳統(tǒng)集中傳動型式,工藝孔型設計及變形制度不靈活,軋機高速運行穩(wěn)定性差,設備空載消耗及輥環(huán)消耗高。4)高速線材終軋機組速度高、結(jié)構(gòu)復雜,對設計、制造和裝配要求極高,創(chuàng)新開發(fā)難度極大,而進口裝備費用高、供貨周期長、備件及維護費用高,嚴重制約國內(nèi)高速線材生產(chǎn)技術的進步與發(fā)展。針對高速線材行業(yè)轉(zhuǎn)型升級存在的核心問題,本項目以高品質(zhì)、低能耗及綠色化線材高速軋機裝備技術為目標,創(chuàng)新性的提出了獨立傳動的模塊化高速軋機裝備技術理念,開發(fā)了全新的線材綠色、低耗獨立傳動式模塊化高速軋機工藝、裝備及控制技術,并實現(xiàn)了產(chǎn)業(yè)化應用,提高了線材生產(chǎn)的靈活性,提升了產(chǎn)品品質(zhì),降低了能耗及生產(chǎn)成本,實現(xiàn)了線材的綠色低耗生產(chǎn)。
圖1 綠色低耗獨立傳動式高速線棒材模塊軋機的研發(fā)技術路線
為解決高速線材行業(yè)所存在的痛點問題,中冶賽迪高速線材技術研發(fā)團隊顛覆傳統(tǒng)的集中傳動技術思維,以獨立傳動的模塊化高速線材生產(chǎn)技術為關鍵,通過對高速獨立傳動軋制過程金屬變形、控軋控冷離線仿真、組織性能調(diào)控、模塊化高速軋制裝備及吐絲裝備、自動化控制等關鍵技術的研究,創(chuàng)新開發(fā)出了全新的線材綠色、低耗獨立傳動式模塊化高速軋機工藝、裝備及控制技術,并實現(xiàn)了產(chǎn)業(yè)化應用。1、基于獨立傳動模塊軋機,開發(fā)了高靈活性、高適應性的孔型系統(tǒng),實現(xiàn)了對線棒高速軋制過程金屬變形的精確控制;探明了高速線材軋制工序軋件傳熱特點,建立了軋制工序軋件換熱模型,開發(fā)了控軋控冷離線仿真模型,實現(xiàn)了高速線材軋制工序溫度仿真;開發(fā)了高速線材及高速棒材柔性化組織性能調(diào)控技術,實現(xiàn)了綠色低耗生產(chǎn)。

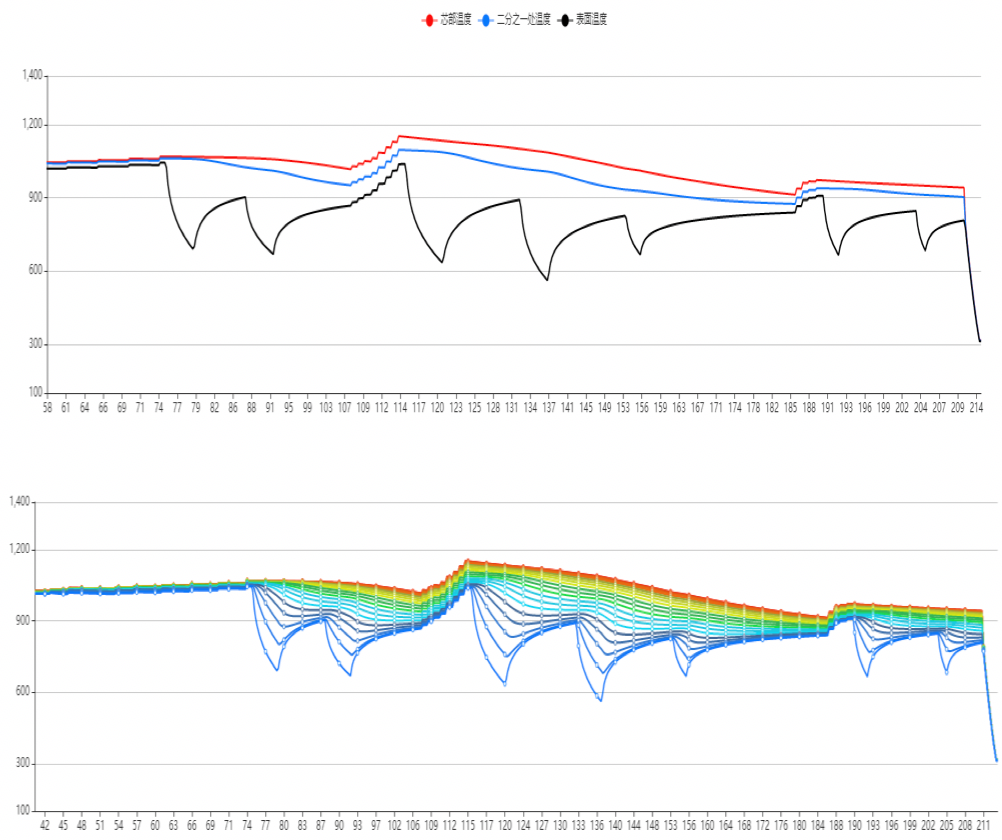
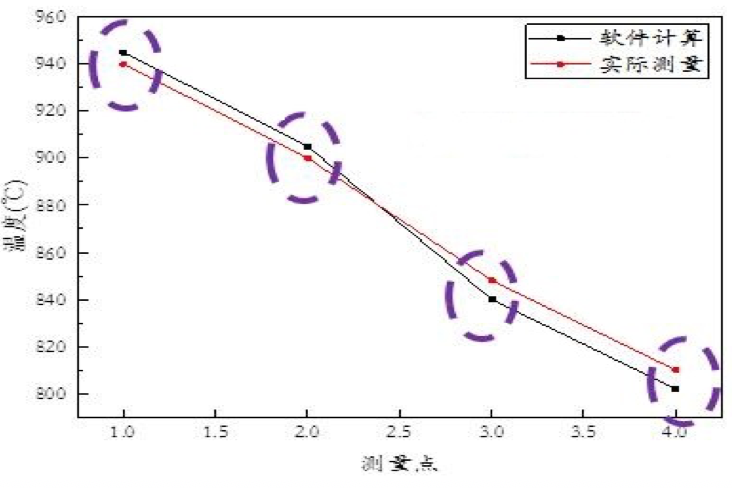
2、創(chuàng)新性提出了高速精軋機雙模塊化理念,開發(fā)出基于獨立傳動的模塊化高速軋機,形成了具有高互換性及高適應性的超重載型250、230及高精度型150標準化軋機,實現(xiàn)了低溫軋制及高精度軋制。開發(fā)了單一速比及多速比齒輪箱,與標準化模塊軋機組合使用,實現(xiàn)了1拖1或1拖2的機組型式,縮短了傳動鏈,簡化了設備結(jié)構(gòu),提高了機組高速運行穩(wěn)定性,消除了空載電耗,降低了輥環(huán)消耗。
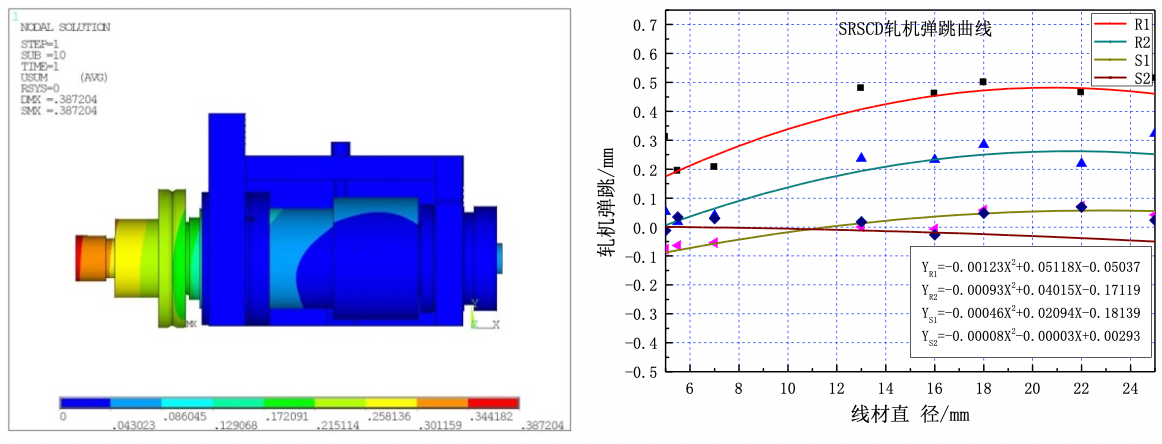
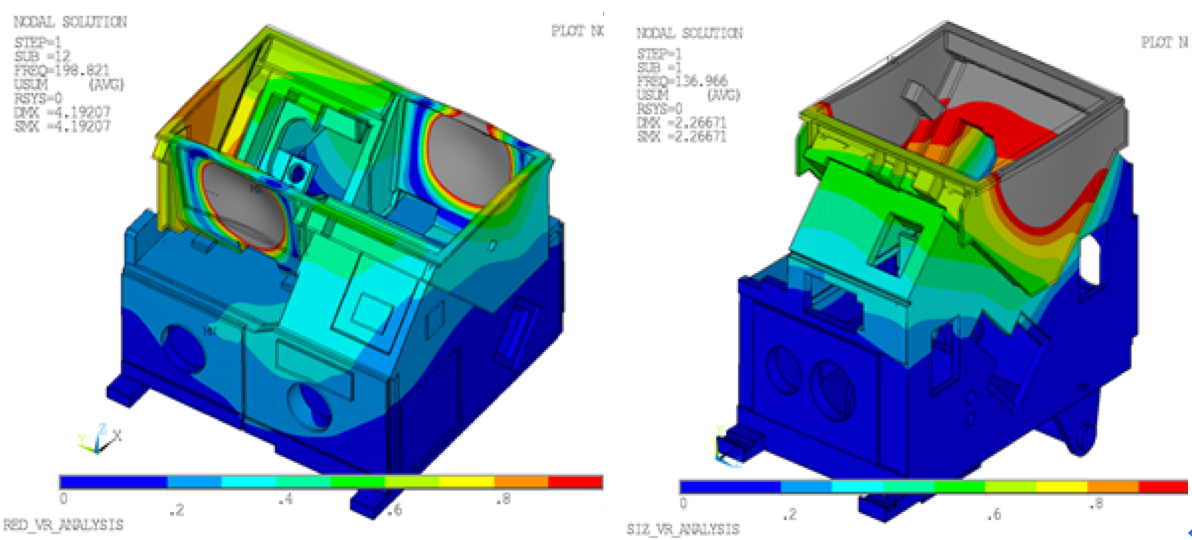
3、建立了吐絲管曲線力能模型,開發(fā)了曲率光滑的吐絲管曲線,降低了線材運行阻力;開發(fā)出吐絲頭非對稱轉(zhuǎn)子動力學分析軟件,實現(xiàn)了吐絲頭輕量化設計,解決了吐絲頭動平衡問題;采用阻尼減振裝置降低了吐絲機的振動幅值。開發(fā)了120m/s的20度傾角吐絲機,可實現(xiàn)更大規(guī)格范圍線材的低溫高速吐絲成圈。
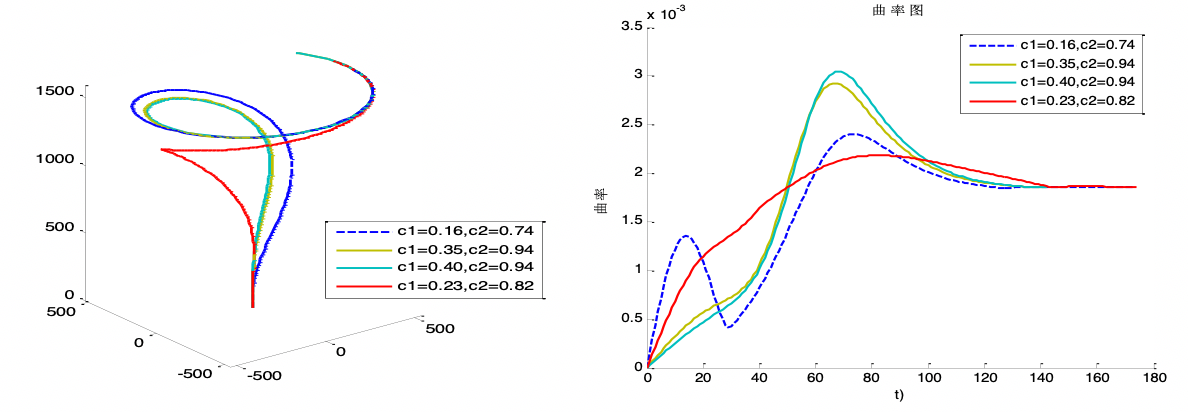
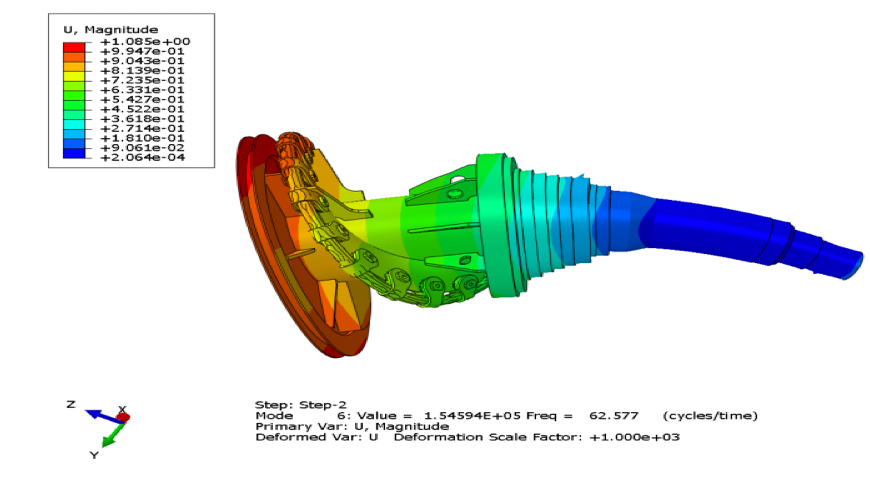
4、開發(fā)了自適應的動態(tài)速降補償技術,消除了高速軋制過程中咬鋼速降對軋制穩(wěn)定性的影響;開發(fā)了多機架速度同步控制技術,替代了傳統(tǒng)集中傳動精軋機的機械同步,保證了高速穩(wěn)定生產(chǎn)。
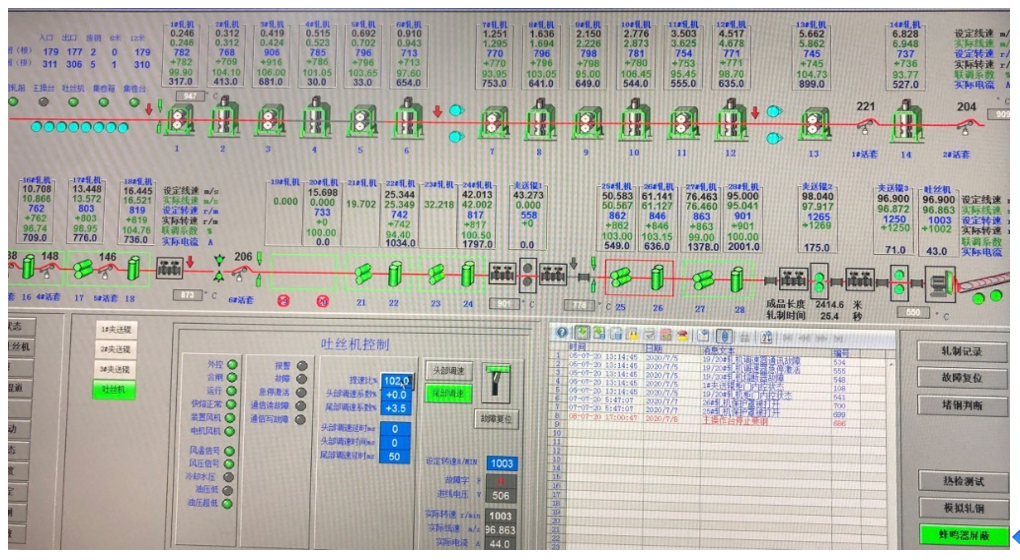
本項目創(chuàng)新技術已成功應用于江蘇亞盛、福建三山、新疆天山及寧夏建龍等國內(nèi)外30余家高速線材及高速棒材企業(yè),產(chǎn)品累計銷售近170臺套。采用該技術實現(xiàn)了高速線棒材的低溫軋制,HRB400E盤螺的錳合金含量降低20%,平均電耗較集中傳動降低約5%,平均輥耗較集中傳動精軋機降低約15%。
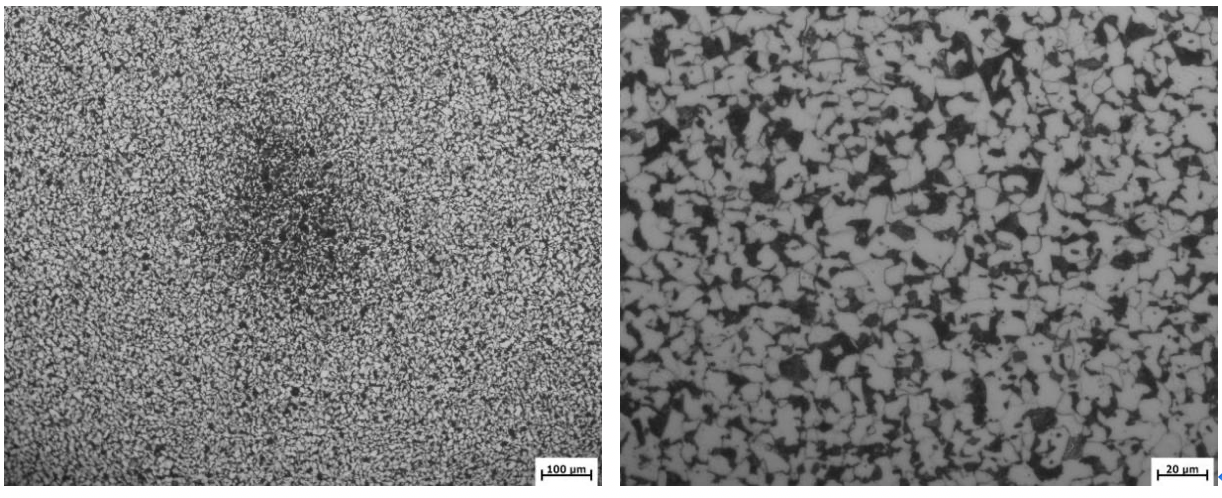

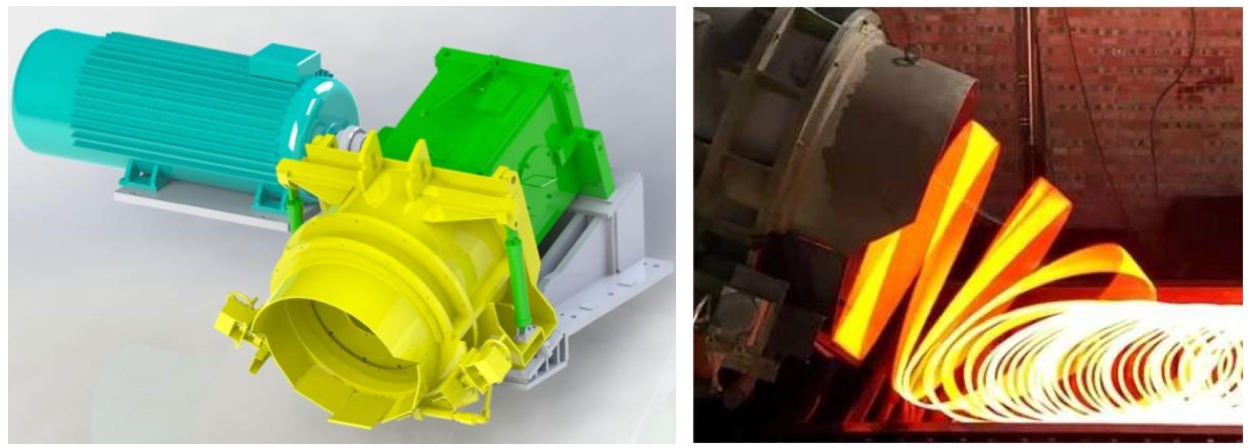
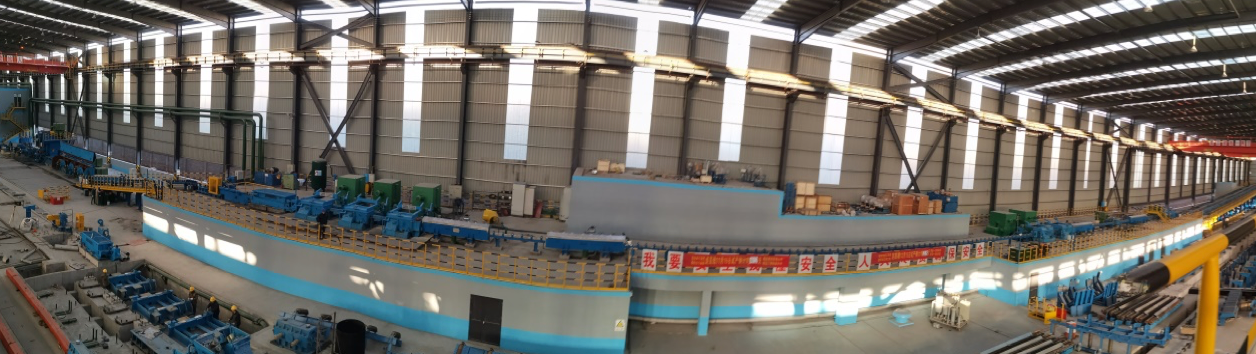
圖13 國內(nèi)首條全模塊化軋機高速線材生產(chǎn)線本項目成果已獲授權專利28項,其中發(fā)明專利9項,申請專利PCT 3項,參編國家標準2項,發(fā)表論文10篇。經(jīng)專家鑒定,本項目成果總體達到國際先進水平,其中開發(fā)的基于獨立傳動模塊化軋機的高速線材柔性化組織性能調(diào)控技術達到國際領先水平。